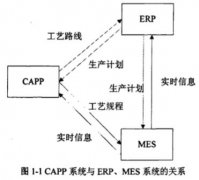
PLM协同CAPP方案
协同CAPP对于缩短敏捷制造企业的产品开发周期、降低产品成本、提高产品质量具有十分重要的理论和现实意义。协同CAPP系统,按其工作的机制,分为信息协同、协同工艺设计、工艺管理三部分
协同CAPP对于缩短敏捷制造企业的产品开发周期、降低产品成本、提高产品质量具有十分重要的理论和现实意义。协同CAPP系统,按其工作的机制,分为信息协同、协同工艺设计、工艺管理三部分内容,信息协同研究CAPP系统与其他系统之间的信息交互,研究CAPP与CAD、ERP、MES等系统的集成;协同工艺设计研究在CAPP系统内部如何实现工艺的协同编制;工艺管理则是研究如何管理协同工艺设计产生以及使用的工艺数据以及工艺设计过程中的流程。
(1)信息协同
在CAPP与CAD系统的集成方面,通过实现CAD与CAPP的柔性化集成,CAD为工艺设计人员提供零件图纸信息、BOM信息和相似零件信息,从而减少了工艺人员的工作量,并且保持数据的一致性。
CAPP与ERP系统集成方面,ERP维护材料库存、设备和工装状况等数据,传递给CAPP。同时,当材料库存、设备和工装状况等数据发生变化时,由ERP完成这些数据的比较,将变更信息、流程控制信息传递给CAPP,以便于CAPP产生的制造BOM(Bill Of Materials)等信息尽量能够符合企业生产实际。
在CAPP中将这些信息进行处理,生成相应的制造BOM、工艺路线等信息,还包括比较得出的结论信息,如哪些信息变更、变更范围等,将其传递给ERP。同时,CAPP系统中将工时、材料等汇总表输出到ERP,使采购、人事、财务的数据更加准确、及时。
CAPP与MES系统集成方面,由于CAPP系统的产品和工艺组织方式与MES中的有所差别,需要将CAPP系统的产品型号与MES系统中的型号相对应,以零部件图号代替节点ID和父节点ID来确定结构树上某一节点的子件图号和父件图号,并在集成模块中建一个产品信息中转表,将CAPP系统中的产品和工艺信息按照MES系统的方式来组织,实现CAPP系统的产品结构和工艺能直接为MES系统所使用。
MES需要的工艺信息可以由CAPP系统产生的工艺文件中筛选并获取。还有的学者研究在加工工艺规划阶段为了保证车间作业调度的可行性和合理性,从车间作业优化调度与控制的角度,研究工序相关性问题及其描述方法,开发面向车间MES的CAPP系统。
除了研究CAPP系统与各独立系统之间的集成外,当前还有研究以PDM、PLM作为集成框架,实现CAPP/CAM/MES/EI冲等系统之间的集成。PDM、PLM系统通过提取工具将CAD的装配表中相关属性信息进行提取,并根据相关装配关系生成设计BOM,创建产品结构,并将其存储在系统数据库中。
设计BOM经过一定转化后可作为工艺BOM以及制造BOM,在产品全生命周期各阶段使用,从而实现工艺与各系统之间的信息交互。在实现方法上,主要是通过建立软件接口实体模块,将CAPP系统提供的文本格式的工艺数据转换成其他系统可用的数据记录。
(2)工艺协同设计
工艺协同设计研究如何有效地支持在地理上分布的多工艺人员同步地开展设计工作,其研究内容主要包括协同CAPP编制同步机制、会话管理机制和系统通信机制等。
工艺协同设计根据协同中参与的人员分为系统内部协同与外部协同两种方式。内部协同为工艺人员之间提供协作环境,工艺设计者之间进行协同设计,协同调度工艺资源。它主要包括工艺设计、工艺管理、工艺输出、协同工作等模块。
外部协同为工艺人员与结构设计者、生产制造与管理者之间提供协作平台,系统外部协同活动由基于Web的工作流系统与电子白板、协同浏览器、共享音频、共享视频、多媒体电子邮件、网络会议等协同使能工具支持。
在实现方法上,有的学者研究基于制造协作网的协同式CAPP系统㈨。在敏捷制造和企业动态联盟的条件下应用协同CAPP(COCAPP)。协同CAPP的体系结构采用B/S三层模式,满足敏捷制造的动态性,建立一个广域分布的、并行的、动态群组工艺规划系统。通过并发控制和加锁机制实现工艺的协同设计。在协同研究领域,还有通过协同软件的方式,实现协同工艺设计。
协同软件的精髓在于搭建一个平台,使管理人员通过相应的权限管理不同系统的数据,让工作在不同地域、不同时间的人员通过平台进行协调沟通,了解工作的进展情况,明确工作的目标。总之通过协同软件,使分布在不同区域的人员在同一个环境下协同工作,实现统一管理。
随着软件、网络与通讯技术的融合以及现代管理组织对敏捷性的要求,协同软件也逐渐暴露了其不足之处,具体表现在虽然实现了交流上的便利,但没有实现针对不同系统具体业务之间的协同,例如,针对CAPP系统中的工艺编制,分布在不同区域的工作人员,通过协同平台只能实现交流上的便利,而不能实现在CAPP系统上工艺文件的互操作,与CAPP系统的结合也不够紧密,满足不了企业对协同CAPP的需要。
(3)工艺管理
在工艺设计过程中,还涉及到CAPP系统中产生的工艺数据、工艺流程等工艺管理。传统CAPP的工艺流程管理是在CAPP系统内部构建流程管理工具,满足企业的需要;工艺数据包括:资源数据、工艺方案等数据。
传统的独立CAPP在客观上造成了信息孤岛的问题,使工艺数据游离于企业信息流之外。虽然解决了工艺问题,但是割裂了应用之间的有机联系,导致企业中的各种应用无联系、功能不连续不完备,并且因为模型异构,数据管理不统一导致了集成的效率低下,一致性维护困难,面向全企业的信息集成难以实现。
传统的资源管理模式,主要是通过资源数据库的形式,其形式与Windows的资源管理器类似,左侧为工装树,右侧为节点属性标签。分别显示工装种类、工装图号、工装名称、规格、数量。
其对生产资源是一种静态的管理方式,没有考虑资源的状态以及动态变化。传统的设备管理信息系统(PMIS),主要功能是设备台帐和档案管理,可以使设备的静态信息规范化、标准化,以便高效、及时、准确的分析处理这些信息。
有的学者通过CAPP/PDM一体化系统的开发,把工艺数据和产品设计的数据一起由一体化系统统一管理。工艺数据直接和产品数据建立关系。减少了CAPP系统功能的重复建设,促进了CAPP与PDM系统的紧密结合。
本文章来自上海御云信息有限公司 : 本文网址: http://www.plmpdm.cn/zxplm/395.html
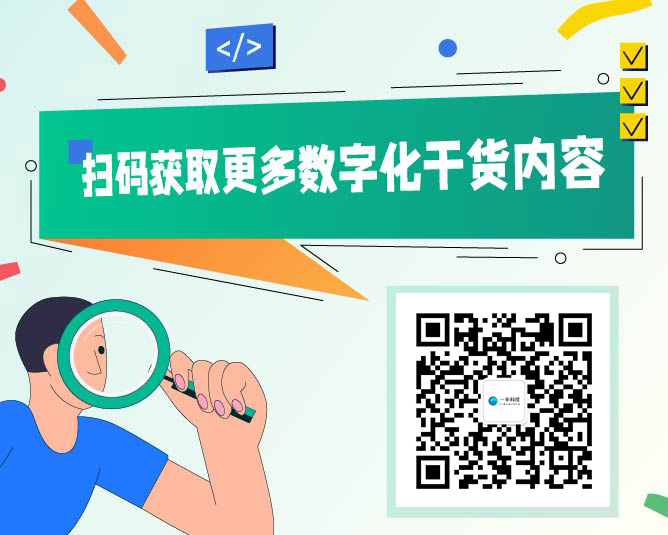