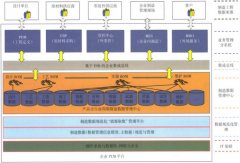
航空行业产品制造企业PLM构建方案
随着制造业信息化的推进,国内一些复杂产品制造企业已先后构建了PDM(产品数据管理)、ERP(企业资源计划)、MES(制造执行系统)、IQS(集成质量系统)、TDM(试验数 据管理)、MRO(维修与保障
产品应用
企业对PLM需求的迫切性
随着制造业信息化的推进,国内一些复杂产品制造企业已先后构建了PDM(产品数据管理)、ERP(企业资源计划)、MES(制造执行系统)、IQS(集成质量系统)、TDM(试验数
据管理)、MRO(维修与保障)等系统,基本实现了企业内各业务过程与数据的信息化管理,已在企业产品研制中发挥了重要作用。但是,由于各业务数据在本业务信息系统管理与保存,且各业务信息系统之间管理数据内容存在重叠、空缺或共享困难等问题,企业信息化整体效益难以显现。下面以航空发动机制造为例,阐述复杂产品制造企业对PLM构建需求的几方面体现。
1管理决策支持
现有PDM、ERP、MES等各信息系统管理着产品不同阶段和不同方面的制造数据,没有形成企业统一和全局的相关数据内容,缺少完整、准确和及时的发动机制造数据的统计和分析,使管理层难以了解整体发动机研制情况,决策缺乏准确的数据支持。
2质量改进支持
影响发动机产品质量的原因可能是多方面的。例如,发动机振动故障的原因很复杂,可能是转子不平衡过大、轴承跳动过大、气流振动过大、局部共振、某连接松动或刮碰等原因,也可能是设计、制造、材料或装配缺陷等造成的。批产与单机试验生产不一样,真正的“试验”体现在批产中。企业需要在批产过程中不断做好制造数据的“积累”,以挖掘产品质量与制造数据分布特征之间的关联“机理”,利用宝贵的制造数据资源支撑航空发动机制造和设计质量的改进。
3质量追溯
产品质量排查和返厂机故障处理是一个耗费人力、物力、财力和时间的综合工程。一次大的故障追溯需要数十人数天时间夜以继日地查阅资料,追查可能涉及数百个件号,其中要排查m缺陷零件对在产、服役发动机和备件的影响面是最大的挑战。
4产品技术状态控制管理
产品研制/定型/批产多型号交叉与并举、不同批次产品技术状态交叉、技术文件变更频繁、现场偏离和超差让步等对发动机产品技术状态控制管理提出更高要求。企业更需要现场技术状态一致性执行的及时、有效和全面的信息支撑通道,使各业务部门了解产品所有技术状态与历史,并能够方便快捷地进行搜索和质量跟踪。
5智力资产管理
企业发动机产品研制活动中会形成智力资产的积累,这既包括企业几十年实践中已沉积的大量相关技术数据和方法,也蕴含着航空人大量的心血和汗水,甚至有些经验教训是用生命换来的。因此,航空发动机研制各个环节的工作依赖于对已有智力资产的继承和创新。
产品全生命周期管理技术明确定位为面向制造企业。南各业务信息系统局部性业务数据管理向企业统一和协同的全局性数据管理转化,工程设计数据管理为主的PDM向涵盖设计、工艺、生产、质量、服务等数据管理的PLM转化,为企业提供一种从整体上实现对产品生命周期中各阶段相关信息、过程和资源进行优化管理的解决方案,是航空发动机制造企业信息化必由之路,也是国内复杂产品制造企业信息化发展过程中面临的重大挑战。
基于多信息系统下的企业PLM构建方法与总体框架
PDM是管理所有与产品相关的信息和过程的技术,应用中偏重于设计(产品、工艺、工装设计等)领域。PLM管理的范围超越PDM的工程领域,扩展到市场、生产、销售及售后等全生命周期,并包括产品全生命周期中所有知识及复用管理。在PDM基础上,PLM延伸到制造、服务等全生命周期管理,并将企业智力资源作为重要管理内容。
1构建方法
以PLM软件为IT框架核心,以企业PDM、ERP、MES、IQS等信息系统的业务过程与数据管理为基础,企业制造数据管理中心将产品制造数据管理整合于统一的平台,以基于BOM的产品数据管理信息模型为数据组织与关联的中枢,以ESB(企业服务总线)为数据交互的桥梁,构建多信息系统网络分布环境下逻辑统一和集成化的企业PLM平台,实现企业从设计、工艺、采购、加工、装配、试车和售后服务等发动机产品全生命周期过程、数据和智力资产的管理。
2总体平台框架
基于多信息系统网络分布环境下的企业PLM平台框架如图1所示,该平台主要通过制造数据管理中心的构建和协同集成方式来实现(说明:实箭头标识为企业园区网内部连接,虚箭头标识为企业园区网与外部制造协同数据的交互)。
(1)以贯穿发动机全生命周期的BOM(设计BOM-工艺BOM-中性BOM-制造BOM-维护BOM)管理为主干进行数据组织、关联和整合,构成以发动机台份实物产品为核心的制造数据管理。
(2)企业管控中心、ERP、MES等业务信息系统通过ESB实现与制造数据管理中心的信息交互和数据归档。
(3)对分散在企业外部的产品制造协同数据(原材料采购、产品设计、外委件制造、客户产品使用等数据)通过企业相应业务管理系统的采集,统一归档到制造数据管理中心,形成一个覆盖航空发动机全生命周期的制造数据管理。
(4)对发动机产品研制过程的制造工程知识进行管理,进而实现企业PLM平台对发动机产品研制过程、数据和智力资产的统一管理。
(5)对发动机产品全生命周期制造数据进行规范化定义与管理,为企业全面实施基于PLM的制造数据管理提供重要基础和保障。
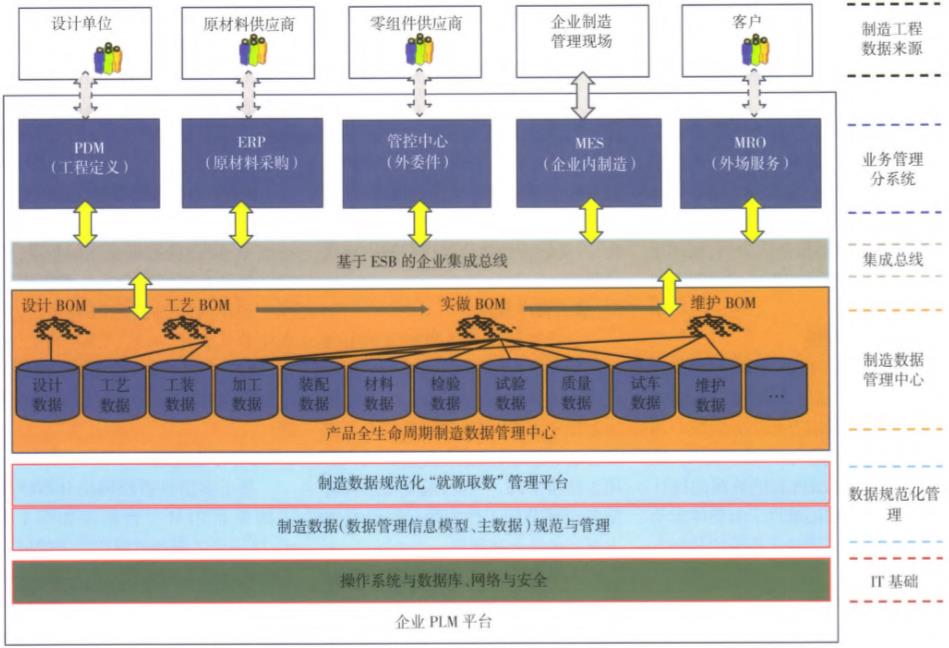
图1 基于多信息系统网络分布环境下的企业PLM平台框架示意图
企业PLM平台实现的关键内容与挑战
在企业PLM平台构建总体框架下,从信息技术视角看,实现企业PLM平台的关键内容是发动机产品数据管理信息模型、数据规范化和数据采集模型定义等。产品数据管理信息模型定义解决数据组织、转化、关联及应用管理的问题;数据规范化解决数据表达一致性和集成共享问题;数据采集模型解决数据来源与维护问题。
1 发动机产品全生命周期数据管理信息模型
发动机研制过程中,大量、多样化及全生命周期产品制造数据的组织、转化、关联和层次管理信息模型是企业PLM平台数据管理实现的核心,是确保企业PLM数据流畅通、数据源唯一、数据统一管理的关键与重要基础。
(1)基于台份BOM的数据组织信息模型。
BOM是研究产品数字化数据的产生、加工、拓延、控制和管理的重要组成部分。BOM是发动机产品数据管理的组织核心,发动机研制过程中产生的各类数据将基于发动机各阶段形态的BOM进行统一管理。
企业PLM制造数据的管理和记录将以台份实物产品为核心进行组织和管理,所管理的数据将包含设计、工艺、工装、加工、装配、材料、检验、试验、质量、试车、维护与服务数据等,不同台份分别记录不同实做零部件所关联的设计数据、工艺数据、制造数据和维护数据等,见图2。
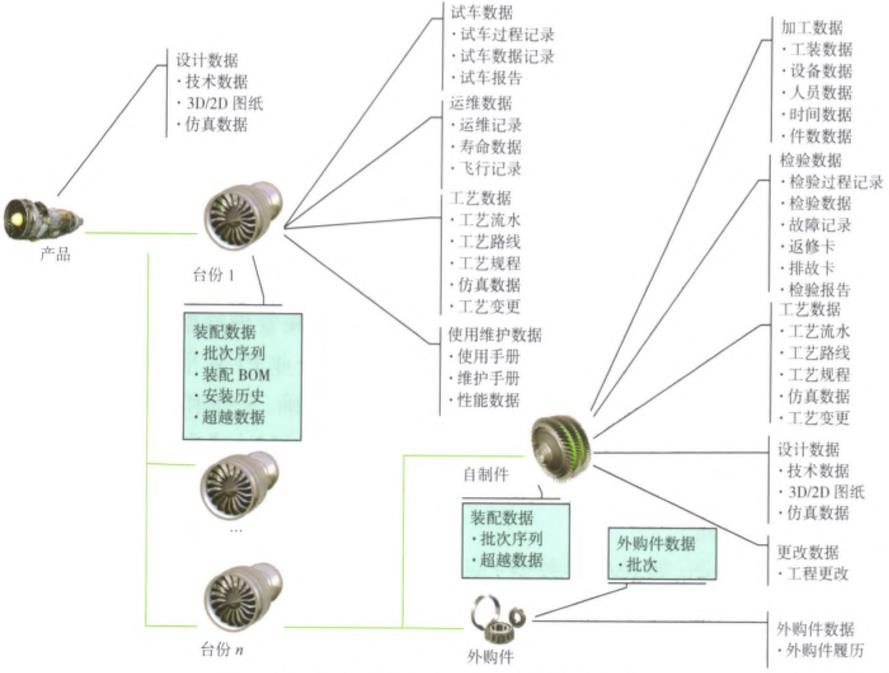
图2 台份BOM数据组织信息模型示意图
(2)BOM的转化和关联信息模型。
BOM信息伴随着产品全生命周期演变和生产经营管理业务域不同而产生、传递和演变,如图3所示。伴随产品在全生命周期过程的变化,BOM经过了设计BOM、工艺BOM、质量(中性)BOM、实物BOM和服务BOM等演变;伴随生产经营管理业务域不同,BOM经过了设计BOM、工艺BOM、制造BOM及由制造BOM衍生的计划BOM、采购BOM、成本BOM等演变。
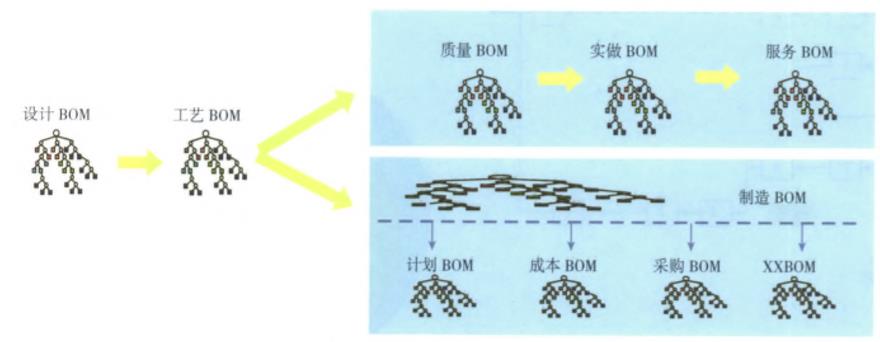
图3 产品BOM产生、传递和演变过程示意图
利用TeamcenterPLM平台数据管理功能,用面向对象的数据管理工具实现设计BOM——工艺BOM——质量(中性)BOM——实做BOM——维护BOM的转化和关联,实现基于BOM的制造实物数据与产品定义虚拟数据的关联与管理,进而实现各阶段发动机产品制造数据之间的横向关联与管理。图4为质量BOM、实物BOM、维护BOM之间转化与关联的信息模型示意图。
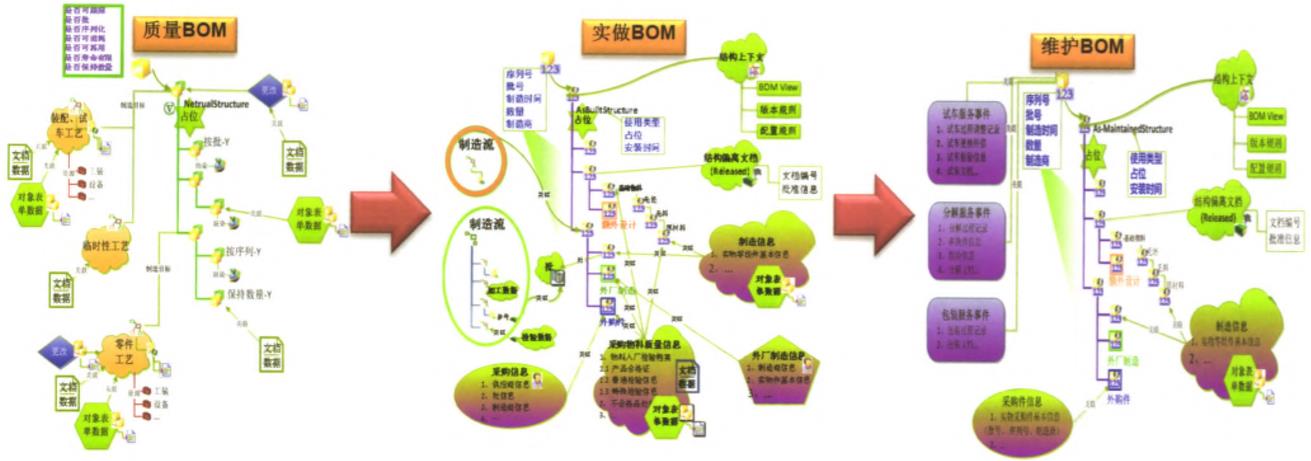
图4 BOM转化与关联管理信息模型示意图
(3)制造流管理信息模型。
零部件在加工/装配过程中经历的所有工序构成一个连续流,即“制造流”。由于企业工艺规程是按不同专业单位分别编制的,同时在零部件加工前可能有工艺超越,在加工过程中可能有返工、返修等临时的工艺卡片,在制造过程中可能有分批的情况发生,因此制造流可能与工艺规程的工序流有较大差异而与真实物流保持一致。制造流管理信息模型如图5所示。
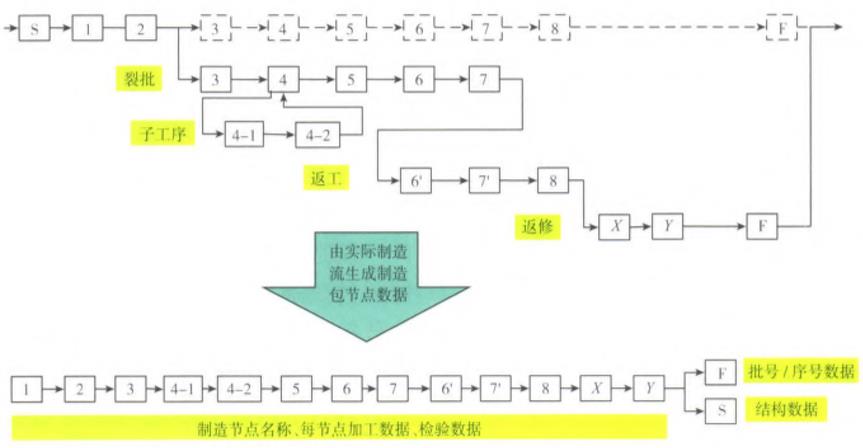
图5 制造流管理信息模型示意图
(4)数据纵向关联管理层次信息模型。
企业制造数据管理中心对发动机制造关键结论数据“直接”管理,并通过系统信息共享机制实现关联的试验和辅助制造信息的查询与利用,将物理上分布的企业产品数据形成逻辑上的统一管理,图6为全局制造数据纵向关联管理的层次信息模型。
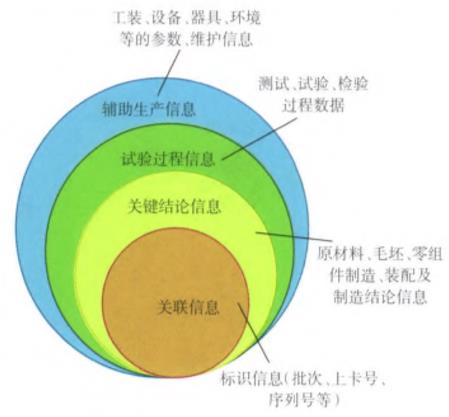
图6 全局制造数据纵向关联管理的层次信息模型
(5)发动机产品全生命周期数据管理。
通过BOM的转化与关联,制造数据管理中心实现各阶段发动机产品制造数据的横向关联管理;通过层次信息管理,实现信息系统间发动机产品制造数据的纵向关联管理;通过将制造流与零部件和制造节点的关联,实现实物BOM——实物零部件。制造流——制造节点——制造过程数据的贯通关联管理。通过上述制造数据的关联管理,可实现发动机产品制造数据的有效组织、差异对比和可追溯性;通过制造流与制造数据的结构化,可实现发动机产品制造过程的质量统计与分析,提供产品质量改进和决策信息。
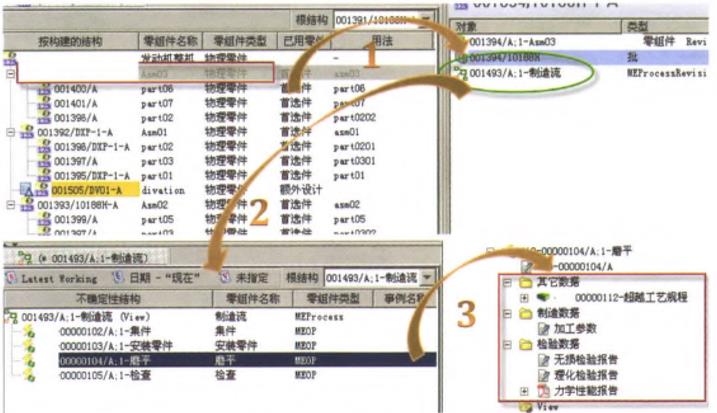
图7 制造数据查询示例
图7是通过实物BOM——实物零部件——批——制造流——制造节点——制造数据关系对产品制造数据查询的示例。图8是通过发动机故障——某位置叶片故障——叶片材料问题一同材料所有实物零件——在制品,在服役,备件查询实现对产品制造质量追溯的示例。
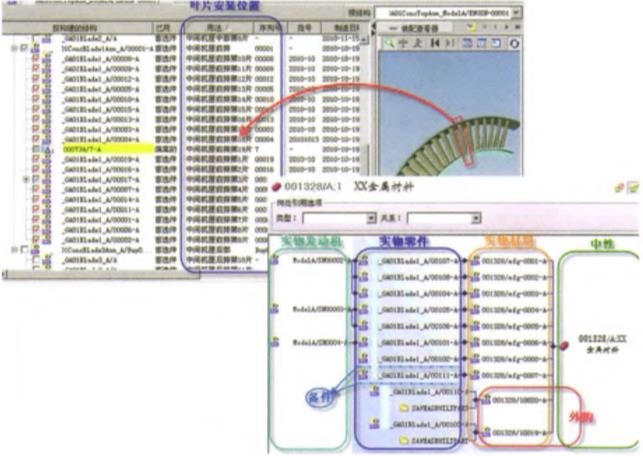
图8 制造质量追溯示例
2 数据规范化
数据规范化是数据模型细化到一定层次时对数据定义的需求。美国著名数据管理专家威廉·德雷尔在专著《数据管理》中总结了数据管理标准化方面的经验,他的名言是:没有卓有成效的数据管理,就没有成功高效的数据处理,更建立不起来整个企业的计算机信息系统。数据不规范,企业PLM制造数据的统一归档、共享和管理就不可能实现。信息化过程要求企业实现流程规范、操作规范和数据规范的统一。
由于复杂产品制造数据具有多样性、多态性及复杂性等,数据规范化成为复杂产品制造企业信息化过程中的一个很大挑战,其中制造集成数据的规范定义与管理是企业PLM实施的重要基础内容。
(1)集成数据的规范定义。
企业PLM集成交互数据的规范定义重点是梳理企业全局业务数据,并结合相关数据实施标准(国家标准、行业标准和企业标准等)来开展相关数据规范定义,其主要工作内容包括:
·面向业务主题的数据管理范围与粒度大纲确定;
·用户视图(如表单类数据)应用分析与分类定义;
·集成交互数据(主数据、业务数据)的规范化定义;
·数据定义、生成、存储、应用和维护方法与制度的建立。
(2)数据规范化管理。
在企业制造数据规范一致性定义和维护制度的基础上,建立用户、用户数据视图、业务数据元素定义、企业(主)数据字典间结构关联关系,借助信息技术构建企业数据规范化管理平台,实现企业“就源取数”规范化管理的落实,其平台架构与关系见图9。
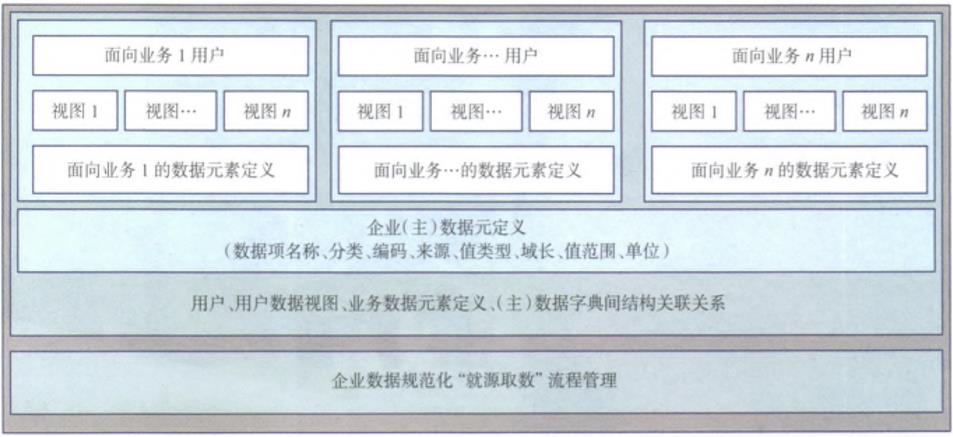
图9 企业规范化“就源取数”管理平台示意图
3 数据采集管理模型
建立企业PLM平台信息系统数据安全、准确、完整和及时性共享与传输机制,通过企业制造数据管理中心实现与ERP、MES、IQS等业务系统的信息集成,实现企业产品制造数据的统一归档、共享和管理。图10为制造数据管理中心与其他业务系统集成数据采集总框架模型,图11为制造数据管理中心与其他业务系
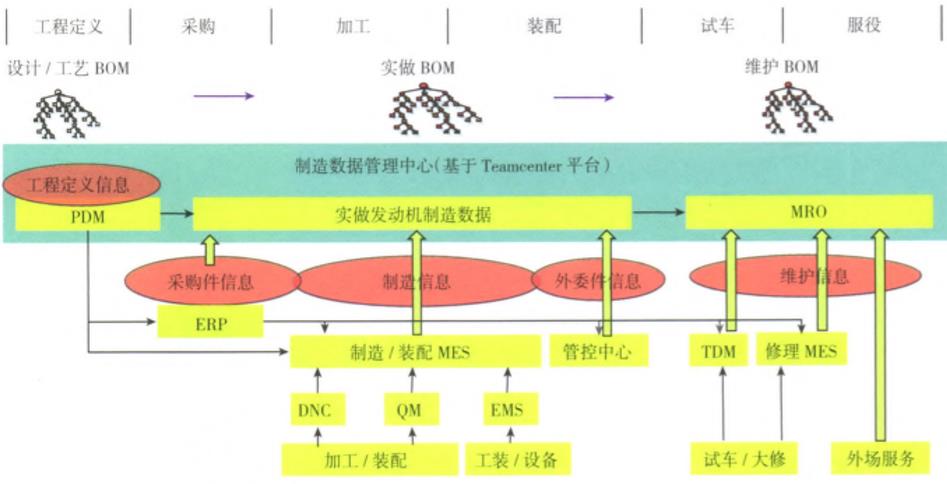
图10 数据采集总框架模型
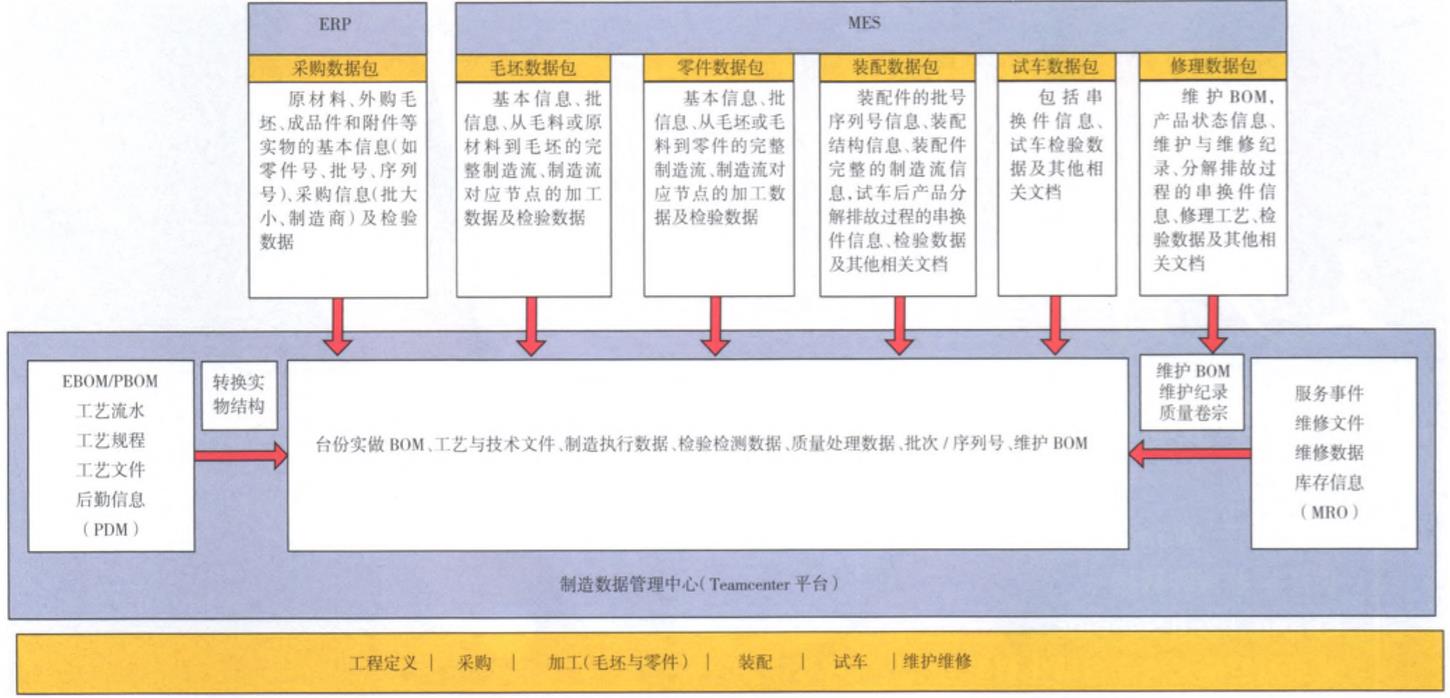
图11 制造数据管理中心与业务信息系统集成采集接口数据
结束语
本文结合航空发动机产品制造企业PLM相关实践的探索,研究了复杂产品制造企业PLM构建方法,重点提出了基于企业多信息系统环境下实现PLM平台的总体思路和框架,并阐述了基于BOM关联的产品数据组织与管理信息模型、基于分布式系统逻辑统一的数据层次关联与采集的管理模型、数据规范化管理等企业PLM实施的关键内容、可行方法和局部示例。大型复杂产品制造企业PLM的实施需要企业顶层规划和系统工程方法,具体实现则还需要对多方面的内容和难点进一步研究,以推进中国制造业信息化建设。
随着制造业信息化的推进,国内一些复杂产品制造企业已先后构建了PDM(产品数据管理)、ERP(企业资源计划)、MES(制造执行系统)、IQS(集成质量系统)、TDM(试验数
据管理)、MRO(维修与保障)等系统,基本实现了企业内各业务过程与数据的信息化管理,已在企业产品研制中发挥了重要作用。但是,由于各业务数据在本业务信息系统管理与保存,且各业务信息系统之间管理数据内容存在重叠、空缺或共享困难等问题,企业信息化整体效益难以显现。下面以航空发动机制造为例,阐述复杂产品制造企业对PLM构建需求的几方面体现。
1管理决策支持
现有PDM、ERP、MES等各信息系统管理着产品不同阶段和不同方面的制造数据,没有形成企业统一和全局的相关数据内容,缺少完整、准确和及时的发动机制造数据的统计和分析,使管理层难以了解整体发动机研制情况,决策缺乏准确的数据支持。
2质量改进支持
影响发动机产品质量的原因可能是多方面的。例如,发动机振动故障的原因很复杂,可能是转子不平衡过大、轴承跳动过大、气流振动过大、局部共振、某连接松动或刮碰等原因,也可能是设计、制造、材料或装配缺陷等造成的。批产与单机试验生产不一样,真正的“试验”体现在批产中。企业需要在批产过程中不断做好制造数据的“积累”,以挖掘产品质量与制造数据分布特征之间的关联“机理”,利用宝贵的制造数据资源支撑航空发动机制造和设计质量的改进。
3质量追溯
产品质量排查和返厂机故障处理是一个耗费人力、物力、财力和时间的综合工程。一次大的故障追溯需要数十人数天时间夜以继日地查阅资料,追查可能涉及数百个件号,其中要排查m缺陷零件对在产、服役发动机和备件的影响面是最大的挑战。
4产品技术状态控制管理
产品研制/定型/批产多型号交叉与并举、不同批次产品技术状态交叉、技术文件变更频繁、现场偏离和超差让步等对发动机产品技术状态控制管理提出更高要求。企业更需要现场技术状态一致性执行的及时、有效和全面的信息支撑通道,使各业务部门了解产品所有技术状态与历史,并能够方便快捷地进行搜索和质量跟踪。
5智力资产管理
企业发动机产品研制活动中会形成智力资产的积累,这既包括企业几十年实践中已沉积的大量相关技术数据和方法,也蕴含着航空人大量的心血和汗水,甚至有些经验教训是用生命换来的。因此,航空发动机研制各个环节的工作依赖于对已有智力资产的继承和创新。
产品全生命周期管理技术明确定位为面向制造企业。南各业务信息系统局部性业务数据管理向企业统一和协同的全局性数据管理转化,工程设计数据管理为主的PDM向涵盖设计、工艺、生产、质量、服务等数据管理的PLM转化,为企业提供一种从整体上实现对产品生命周期中各阶段相关信息、过程和资源进行优化管理的解决方案,是航空发动机制造企业信息化必由之路,也是国内复杂产品制造企业信息化发展过程中面临的重大挑战。
基于多信息系统下的企业PLM构建方法与总体框架
PDM是管理所有与产品相关的信息和过程的技术,应用中偏重于设计(产品、工艺、工装设计等)领域。PLM管理的范围超越PDM的工程领域,扩展到市场、生产、销售及售后等全生命周期,并包括产品全生命周期中所有知识及复用管理。在PDM基础上,PLM延伸到制造、服务等全生命周期管理,并将企业智力资源作为重要管理内容。
1构建方法
以PLM软件为IT框架核心,以企业PDM、ERP、MES、IQS等信息系统的业务过程与数据管理为基础,企业制造数据管理中心将产品制造数据管理整合于统一的平台,以基于BOM的产品数据管理信息模型为数据组织与关联的中枢,以ESB(企业服务总线)为数据交互的桥梁,构建多信息系统网络分布环境下逻辑统一和集成化的企业PLM平台,实现企业从设计、工艺、采购、加工、装配、试车和售后服务等发动机产品全生命周期过程、数据和智力资产的管理。
2总体平台框架
基于多信息系统网络分布环境下的企业PLM平台框架如图1所示,该平台主要通过制造数据管理中心的构建和协同集成方式来实现(说明:实箭头标识为企业园区网内部连接,虚箭头标识为企业园区网与外部制造协同数据的交互)。
(1)以贯穿发动机全生命周期的BOM(设计BOM-工艺BOM-中性BOM-制造BOM-维护BOM)管理为主干进行数据组织、关联和整合,构成以发动机台份实物产品为核心的制造数据管理。
(2)企业管控中心、ERP、MES等业务信息系统通过ESB实现与制造数据管理中心的信息交互和数据归档。
(3)对分散在企业外部的产品制造协同数据(原材料采购、产品设计、外委件制造、客户产品使用等数据)通过企业相应业务管理系统的采集,统一归档到制造数据管理中心,形成一个覆盖航空发动机全生命周期的制造数据管理。
(4)对发动机产品研制过程的制造工程知识进行管理,进而实现企业PLM平台对发动机产品研制过程、数据和智力资产的统一管理。
(5)对发动机产品全生命周期制造数据进行规范化定义与管理,为企业全面实施基于PLM的制造数据管理提供重要基础和保障。
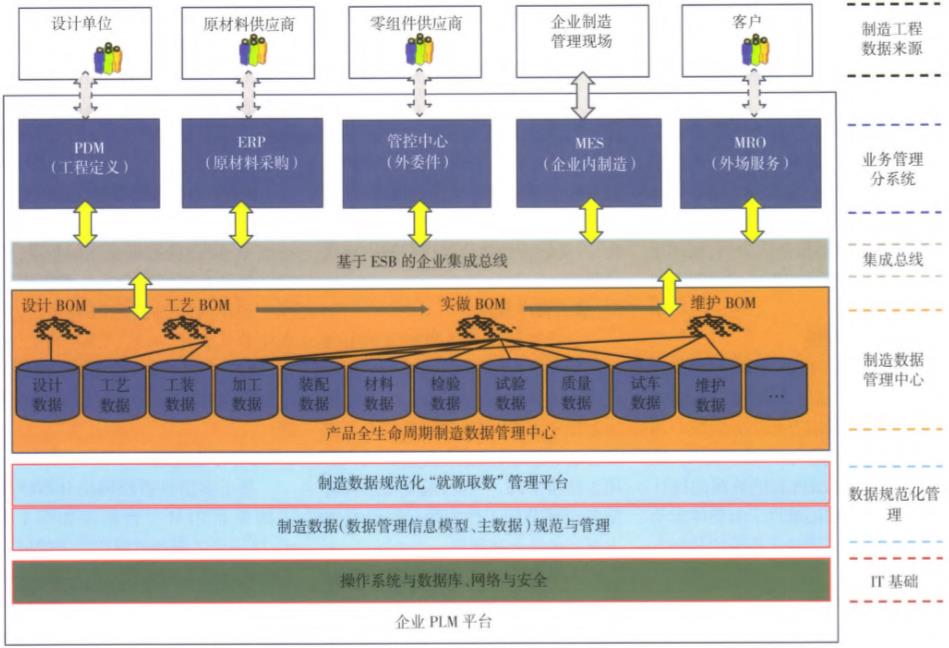
图1 基于多信息系统网络分布环境下的企业PLM平台框架示意图
企业PLM平台实现的关键内容与挑战
在企业PLM平台构建总体框架下,从信息技术视角看,实现企业PLM平台的关键内容是发动机产品数据管理信息模型、数据规范化和数据采集模型定义等。产品数据管理信息模型定义解决数据组织、转化、关联及应用管理的问题;数据规范化解决数据表达一致性和集成共享问题;数据采集模型解决数据来源与维护问题。
1 发动机产品全生命周期数据管理信息模型
发动机研制过程中,大量、多样化及全生命周期产品制造数据的组织、转化、关联和层次管理信息模型是企业PLM平台数据管理实现的核心,是确保企业PLM数据流畅通、数据源唯一、数据统一管理的关键与重要基础。
(1)基于台份BOM的数据组织信息模型。
BOM是研究产品数字化数据的产生、加工、拓延、控制和管理的重要组成部分。BOM是发动机产品数据管理的组织核心,发动机研制过程中产生的各类数据将基于发动机各阶段形态的BOM进行统一管理。
企业PLM制造数据的管理和记录将以台份实物产品为核心进行组织和管理,所管理的数据将包含设计、工艺、工装、加工、装配、材料、检验、试验、质量、试车、维护与服务数据等,不同台份分别记录不同实做零部件所关联的设计数据、工艺数据、制造数据和维护数据等,见图2。
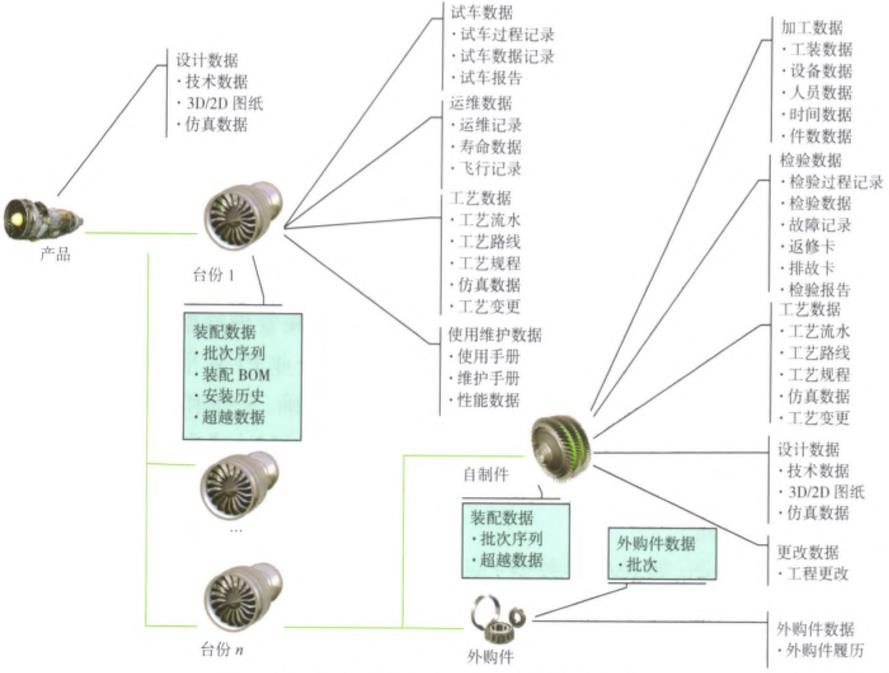
图2 台份BOM数据组织信息模型示意图
(2)BOM的转化和关联信息模型。
BOM信息伴随着产品全生命周期演变和生产经营管理业务域不同而产生、传递和演变,如图3所示。伴随产品在全生命周期过程的变化,BOM经过了设计BOM、工艺BOM、质量(中性)BOM、实物BOM和服务BOM等演变;伴随生产经营管理业务域不同,BOM经过了设计BOM、工艺BOM、制造BOM及由制造BOM衍生的计划BOM、采购BOM、成本BOM等演变。
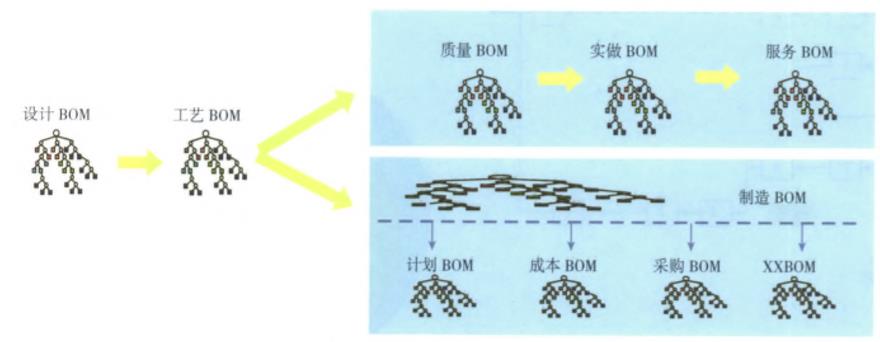
图3 产品BOM产生、传递和演变过程示意图
利用TeamcenterPLM平台数据管理功能,用面向对象的数据管理工具实现设计BOM——工艺BOM——质量(中性)BOM——实做BOM——维护BOM的转化和关联,实现基于BOM的制造实物数据与产品定义虚拟数据的关联与管理,进而实现各阶段发动机产品制造数据之间的横向关联与管理。图4为质量BOM、实物BOM、维护BOM之间转化与关联的信息模型示意图。
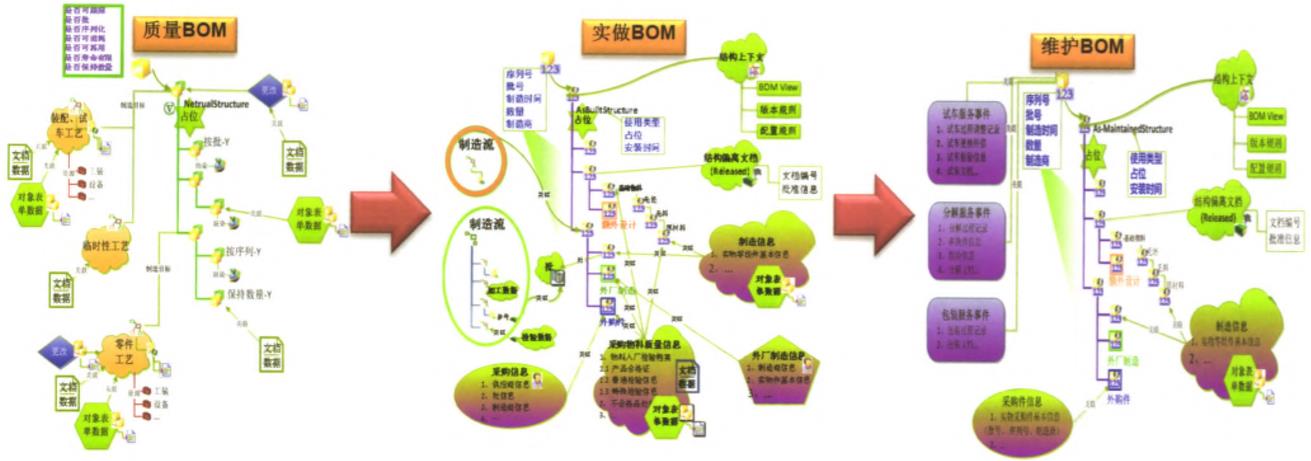
图4 BOM转化与关联管理信息模型示意图
(3)制造流管理信息模型。
零部件在加工/装配过程中经历的所有工序构成一个连续流,即“制造流”。由于企业工艺规程是按不同专业单位分别编制的,同时在零部件加工前可能有工艺超越,在加工过程中可能有返工、返修等临时的工艺卡片,在制造过程中可能有分批的情况发生,因此制造流可能与工艺规程的工序流有较大差异而与真实物流保持一致。制造流管理信息模型如图5所示。
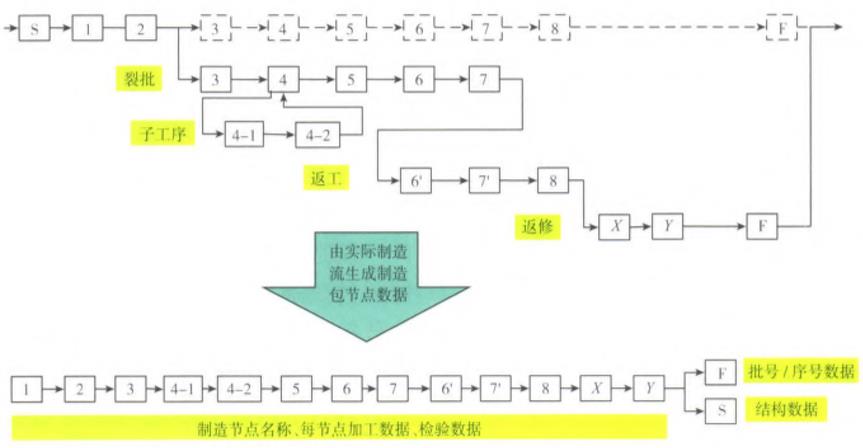
图5 制造流管理信息模型示意图
(4)数据纵向关联管理层次信息模型。
企业制造数据管理中心对发动机制造关键结论数据“直接”管理,并通过系统信息共享机制实现关联的试验和辅助制造信息的查询与利用,将物理上分布的企业产品数据形成逻辑上的统一管理,图6为全局制造数据纵向关联管理的层次信息模型。
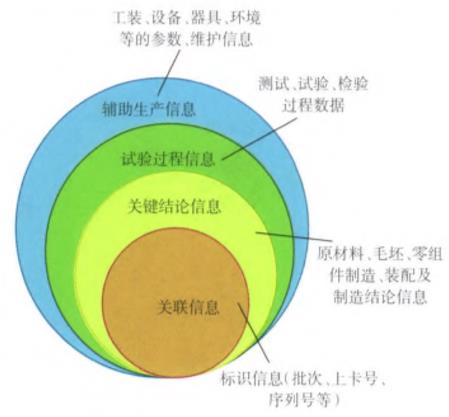
图6 全局制造数据纵向关联管理的层次信息模型
(5)发动机产品全生命周期数据管理。
通过BOM的转化与关联,制造数据管理中心实现各阶段发动机产品制造数据的横向关联管理;通过层次信息管理,实现信息系统间发动机产品制造数据的纵向关联管理;通过将制造流与零部件和制造节点的关联,实现实物BOM——实物零部件。制造流——制造节点——制造过程数据的贯通关联管理。通过上述制造数据的关联管理,可实现发动机产品制造数据的有效组织、差异对比和可追溯性;通过制造流与制造数据的结构化,可实现发动机产品制造过程的质量统计与分析,提供产品质量改进和决策信息。
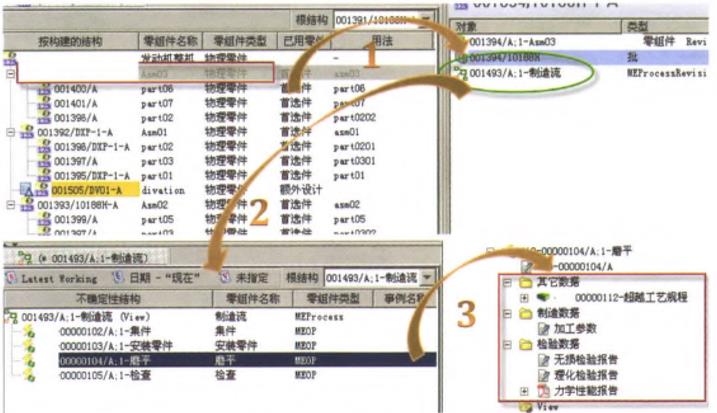
图7 制造数据查询示例
图7是通过实物BOM——实物零部件——批——制造流——制造节点——制造数据关系对产品制造数据查询的示例。图8是通过发动机故障——某位置叶片故障——叶片材料问题一同材料所有实物零件——在制品,在服役,备件查询实现对产品制造质量追溯的示例。
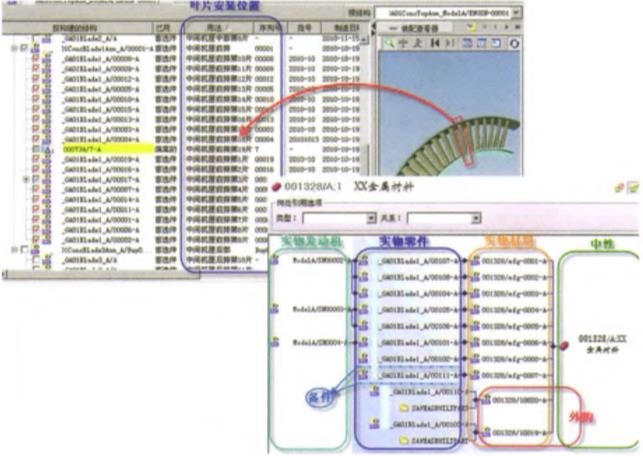
图8 制造质量追溯示例
2 数据规范化
数据规范化是数据模型细化到一定层次时对数据定义的需求。美国著名数据管理专家威廉·德雷尔在专著《数据管理》中总结了数据管理标准化方面的经验,他的名言是:没有卓有成效的数据管理,就没有成功高效的数据处理,更建立不起来整个企业的计算机信息系统。数据不规范,企业PLM制造数据的统一归档、共享和管理就不可能实现。信息化过程要求企业实现流程规范、操作规范和数据规范的统一。
由于复杂产品制造数据具有多样性、多态性及复杂性等,数据规范化成为复杂产品制造企业信息化过程中的一个很大挑战,其中制造集成数据的规范定义与管理是企业PLM实施的重要基础内容。
(1)集成数据的规范定义。
企业PLM集成交互数据的规范定义重点是梳理企业全局业务数据,并结合相关数据实施标准(国家标准、行业标准和企业标准等)来开展相关数据规范定义,其主要工作内容包括:
·面向业务主题的数据管理范围与粒度大纲确定;
·用户视图(如表单类数据)应用分析与分类定义;
·集成交互数据(主数据、业务数据)的规范化定义;
·数据定义、生成、存储、应用和维护方法与制度的建立。
(2)数据规范化管理。
在企业制造数据规范一致性定义和维护制度的基础上,建立用户、用户数据视图、业务数据元素定义、企业(主)数据字典间结构关联关系,借助信息技术构建企业数据规范化管理平台,实现企业“就源取数”规范化管理的落实,其平台架构与关系见图9。
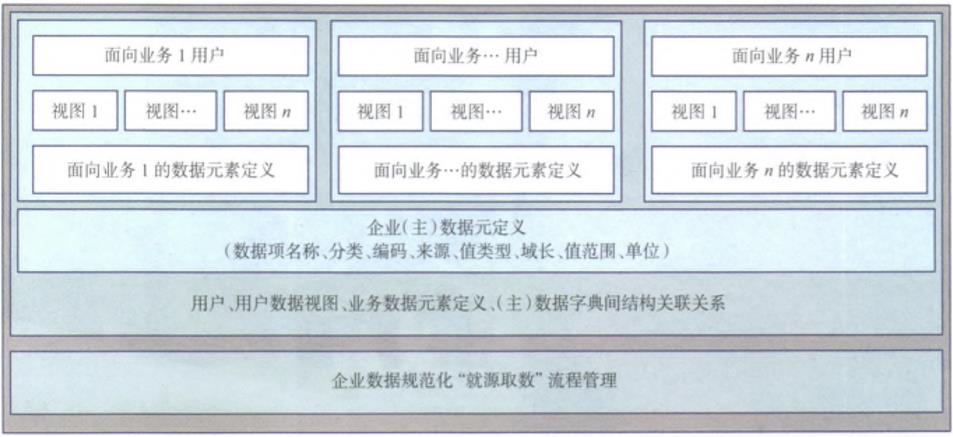
图9 企业规范化“就源取数”管理平台示意图
3 数据采集管理模型
建立企业PLM平台信息系统数据安全、准确、完整和及时性共享与传输机制,通过企业制造数据管理中心实现与ERP、MES、IQS等业务系统的信息集成,实现企业产品制造数据的统一归档、共享和管理。图10为制造数据管理中心与其他业务系统集成数据采集总框架模型,图11为制造数据管理中心与其他业务系
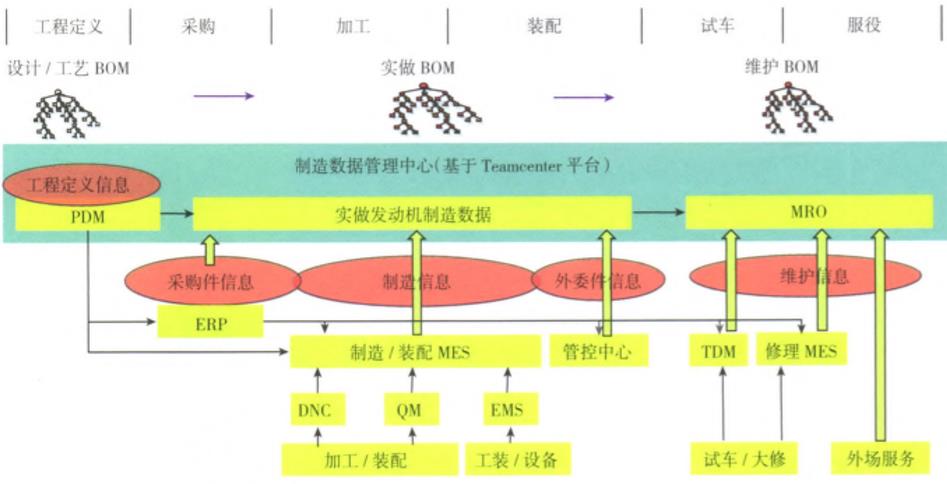
图10 数据采集总框架模型
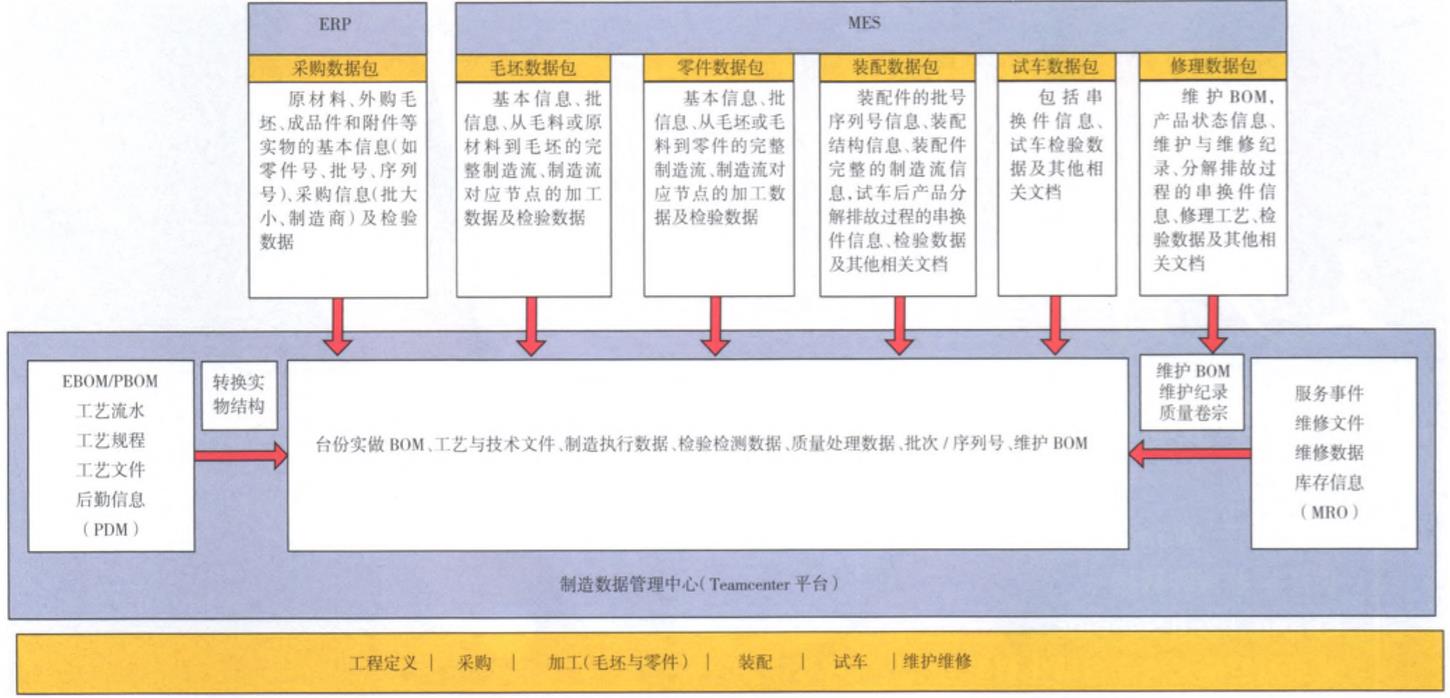
图11 制造数据管理中心与业务信息系统集成采集接口数据
结束语
本文结合航空发动机产品制造企业PLM相关实践的探索,研究了复杂产品制造企业PLM构建方法,重点提出了基于企业多信息系统环境下实现PLM平台的总体思路和框架,并阐述了基于BOM关联的产品数据组织与管理信息模型、基于分布式系统逻辑统一的数据层次关联与采集的管理模型、数据规范化管理等企业PLM实施的关键内容、可行方法和局部示例。大型复杂产品制造企业PLM的实施需要企业顶层规划和系统工程方法,具体实现则还需要对多方面的内容和难点进一步研究,以推进中国制造业信息化建设。
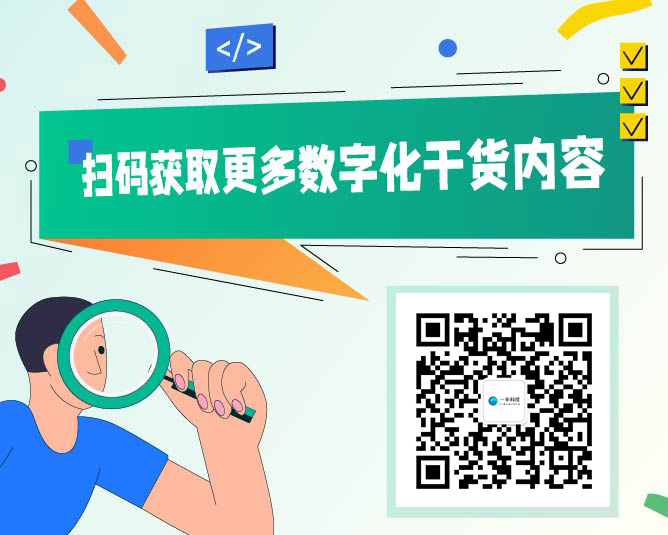