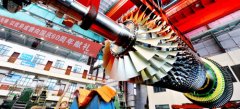
汽轮机装配制造行业PLM解决案例
东方汽轮机厂创建于 1966年,是我国研究、设计、制造大型电站汽轮机的高新技术国有骨干企业和四川省重大技术装备制造基地的龙头企业。工厂位于美丽富饶的四川成都平原西部、德
产品应用
东方汽轮机厂创建于 1966年,是我国研究、设计、制造大型电站汽轮机的高新技术国有骨干企业和四川省重大技术装备制造基地的龙头企业。工厂位于美丽富饶的四川成都平原西部、德阳市郊,占地137万平方米。作为机械工业100强和全国三大汽轮机制造基地之一,企业现有总资产逾80亿元和7000余名员工,专业技术人员2500余名,中高级人员占48%,主要生产设备2400余台,其中大、精、稀设备和数控机床近400台。
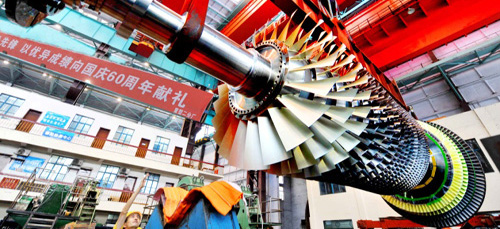
经过30多年的建设发展,工厂现已具备了20万、30万、60万以及百万千瓦等级火电汽轮机、核电汽轮机开发研制和批量生产的综合实力。自建厂以来,工厂已累计生产了500余台各种类型汽轮机共6200余万千瓦,国内市场占有率超过20%。其产品遍及全国各地并出口马来西亚、印度尼西亚、伊朗、孟加拉、巴基斯坦等国家,其产品质量、技术水平和使用性能均受国内外用户普遍好评。
东汽坚持实施自主开发与引进技术相结合的高起点发展战略,大力推进主导产品结构调整和升级换代。目前为止,东汽人自主开发研制的 30万国产化机组已经形成第10代系列并成为省部级优质产品和名牌机组。
东汽与日立公司联合开发研制的亚临界60万机组已经形成批量生产能力,其国产化率达到80%。工厂正与美国 GE公司、法国ALSTOM公司和日本日立、三菱、东芝公司等国际著名大公司进行广泛经济技术合作,努力开发研制超临界、超超临界大功率汽轮机、核电汽轮机、重型燃气轮机以及蒸汽燃气联合循环机组,从而使企业成为世界大型发电制造厂商与核电俱乐部的一个重要成员。
如今,东汽与德国REpower公司又正式签订了技术转让合作协议,在国内率先进入了风电开发新领域。与此同时,东汽与三菱公司联合研制的首台高国产化率重型燃气轮机已经试车成功,并已顺利发货交付用户使用并已投入批量生产。
东汽还本着一业为主,多种经营的发展战略,其产品产业已经辐射到军工、化工、环保、自动控制、表面工程、建筑、运输等领域,进一步提高了生产规模和经济效益并实现企业的做大做强。
东汽与日立公司联合开发研制的亚临界60万机组已经形成批量生产能力,其国产化率达到80%。工厂正与美国 GE公司、法国ALSTOM公司和日本日立、三菱、东芝公司等国际著名大公司进行广泛经济技术合作,努力开发研制超临界、超超临界大功率汽轮机、核电汽轮机、重型燃气轮机以及蒸汽燃气联合循环机组,从而使企业成为世界大型发电制造厂商与核电俱乐部的一个重要成员。
如今,东汽与德国REpower公司又正式签订了技术转让合作协议,在国内率先进入了风电开发新领域。与此同时,东汽与三菱公司联合研制的首台高国产化率重型燃气轮机已经试车成功,并已顺利发货交付用户使用并已投入批量生产。
东汽还本着一业为主,多种经营的发展战略,其产品产业已经辐射到军工、化工、环保、自动控制、表面工程、建筑、运输等领域,进一步提高了生产规模和经济效益并实现企业的做大做强。
近年来,东汽始终坚持以改革为动力,以市场为导向,努力开拓,锐意创新,在产品开发、技术进步、生产组织、经营管理等方面打造了一片新天地,为企业的可持续和跨越发展提供了可靠保障,并实现了汽轮机产量的连年翻番。
2004年工厂汽轮机产量又迈过千万千瓦大关,已经达到1477万千瓦,实现了历史性重大突破。这标志着东汽的综合实力和生产建设登上了更高台阶,东汽人有志气并有能力为祖国电力事业做出更大的贡献。
2004年工厂汽轮机产量又迈过千万千瓦大关,已经达到1477万千瓦,实现了历史性重大突破。这标志着东汽的综合实力和生产建设登上了更高台阶,东汽人有志气并有能力为祖国电力事业做出更大的贡献。
一、东汽信息化总体规划
随着经济发展和科技进步,东汽加强信息化建设,坚持以信息化带动工业化、以工业化促进信息化,有效促进了企业的快速发展。在此期间,工厂先后配备了 SGI工作站、各种PC机及企业服务器,在企业内部广泛应用CAD/CAE/CAM/CAPP/PDM技术,以提高研发质量并缩短产品生产制造周期。
同时将计算机及信息技术广泛应用于财务、人事、采购、产品研发、生产制造和经营管理,工厂独立自主开发出了具有自主版权的产品数据管理系统(PDM)。
为了应对入世挑战并坚持与国际惯例接轨,工厂积极实施企业资源计划(ERP)工程,进一步推进了企业内部物流、信息流、资金流的全面管理,之后实施了plm系统,对设计与工艺管理系统进行全面整合,形成了统一的设计管理平台,提高了企业快速反应能力,增强了企业核心竞争力。
企业先后被国家科技部评为“全国CAD应用工程示范企业”、“国家863计划CIMS应用示范企业”、“国家首批十三家制造业信息化示范工程(MIE)重点建设试点企业”和“四川省制造业信息化示范企业”。
同时将计算机及信息技术广泛应用于财务、人事、采购、产品研发、生产制造和经营管理,工厂独立自主开发出了具有自主版权的产品数据管理系统(PDM)。
为了应对入世挑战并坚持与国际惯例接轨,工厂积极实施企业资源计划(ERP)工程,进一步推进了企业内部物流、信息流、资金流的全面管理,之后实施了plm系统,对设计与工艺管理系统进行全面整合,形成了统一的设计管理平台,提高了企业快速反应能力,增强了企业核心竞争力。
企业先后被国家科技部评为“全国CAD应用工程示范企业”、“国家863计划CIMS应用示范企业”、“国家首批十三家制造业信息化示范工程(MIE)重点建设试点企业”和“四川省制造业信息化示范企业”。
通过PLM系统的实施,整合东汽原有的工程BOM管理系统、部套目录管理系统、数据集成PDM系统、信息共享平台系统,最终替代现有工艺系统,实现东汽设计与工艺一体化管理的系统平台,大力提升信息系统的集成度,PLM系统与ERP系统将作为东汽主要的两大信息系统,是构建大东汽的总体信息化规划蓝图。
二、东汽PLM系统建设
1. 找准症结
在实施PLM系统之前,东汽已经实施oracle EPR系统多年,并自主研发的多个信息系统,已经具备较高的信息化管理水平,但自主研发的信息系统是根据当时的条件和管理要求进行自主研发,存在相应的局限性,不适应东汽在新时期、新条件下的发展,其弊端主要体现在以下方面:
1) 基础数据管理:手工管理方式,纸质图纸成为企业最权威、最有效的数据,电子数据有效性无法保证,版本控制力度低,数据查询、共享与备份烦琐,不利于知识积累和管理效率的提升,已经不能跟进工厂新的发展要求,质量、效率得不到有效保证。亟待提升电子化管理水平,推行并行作业电子化流程,提高过程无纸化管理的程度。
2) 核心问题BOM:零件与文档,设计BOM与制造BOM在技术与制造部门间存在理解差异,必须统一东汽各部门对BOM的理解并做好BOM在各部门的传递,为生产系统提供有效、正确的BOM数据,是保障生产计划正常运行的重要前提。
3) 多工艺路线管理:针对汽轮机产品庞大、结构复杂、单件单台份多场地生产特点,根据汽轮机制造业务及管理现状,解决台份化多工艺路线的管理难题。
4) 项目管理与流程管理:总师办技术准备计划采用人工项目管理,流程采用制度规定,项目管理难度大,效率低,对绩效考核要素不能进行实时、动态的管控。
5) 信息系统管理与集成:东汽信息化建设各模块与各部门之间存在集成孤岛,维护和开发工作量大,信息集成度较低,数据的准确性、完整性和实时性不能得到有效保证,系统间数据传递效率低。同时,业务部门之间不能形成顺畅的业务流程,数据更改无法保证一致。
正视现实问题,东汽厂06年初成立PLM项目选型小组,经多方实地考察和论证,工厂高层站在务实,切实的角度考虑,最终于07年6月引进TiPLM系统,依托此契机,建立东汽厂设计与制造技术统一技术管理平台,提高管理水平。
2. 明确目标
针对东汽厂的现实问题,总体方针是通过PLM系统实施与开发,在东汽建立高效的产品全生命周期管理集成平台,统一管理产品全生命周期各过程以及过程中产生的数据,实现设计、工艺、制造过程的并行,实现设计、工艺、制造数据的流转与管理,实现产品工艺编制、工艺数据与工艺资源的管理,实现与东汽ERP系统的集成。主要目标为:
1) 建立产品研发及制造技术统一集中的产品数据管理框架,解决东汽电子数据安全管理、数据备份及数据容灾问题;
2) 建立产品图纸、文件、BOM及相关数据的电子化共享环境,提高电子数据的权威性和继承性,实现知识库的管理;
3) 优化数据变更管理,保证电子数据的完整性,电子数据与纸质数据的一致性,减少蓝图发放数量,最终实现图、文档及BOM管理过程的无纸化;
4) 加强新增物料控制,在统一的资源管理基础上,逐步减少物料种类,控制和避免一物多码问题;
5) 实现东汽数据归档评审、变更控制与数据发布电子化流程管理,优化业务流程,推进并行工程,提高流程管理效率;
6) 优化东汽设计BOM与制造BOM管理管理,减少设计BOM到制造BOM转换过程中的人工干预,提高BOM转换效率并减少转换差错率,提高设计BOM到制造BOM转换与变更时基础信息的可继承性,最终实现设计BOM与制造BOM流程的贯通,完成PLM与ERP在制造BOM基础上的集成应用;
7) 搭建东汽工程项目管理平台,建立项目管理机制,提高项目管理与水平;
8) 实现多工艺路线管理;
9) 解决装箱BOM管理问题;
10) 优化信息系统管理框架,减少多个异构系统数据集成、系统开发与系统维护问题,实现东汽设计与工艺一体化管理。
3. 锁定范围
东汽PLM项目实施范围主要包括产品开发处、制造技术处、物质管理处、生产协作处、档案管、各分厂及子公司。其中产品开发处主要管理各专业室产生的图纸文档电子数据、设计BOM结构、设计审签、变更与发布业务流程以及产品开发工程项目等;制造技术处主要管理工艺图纸文档、制造BOM结构、毛坯及材料定额、工艺路线及流程等。前期主要以产品开发处和制造技术处为中心,逐步辐射到其它业务部门及子公司,包括风电事业部、自控公司、表面工程公司。
4. 谋划策略
系统实施遵循总体规划分布实施原则,实施周期12个月,主要分为四个阶段:系统调研与总体规划、系统建模与联调、系统试运行与总体评估、系统全面上线。
系统总体规划阶段:07年9月-07年11月 ,主要开展:
1) 系统详细需求调研;
2) 系统测试环境部署;
3) 系统工作原理与基本功能培训;
4) 信息系统整合规划及系统集成方案讨论与评审;
5) 关键业务方案讨论与评审;
6) 总体规划方案评审;
系统建模与联调阶段:07年11月-08年1月底 主要开展:
1) PLM系统基础运行模型搭建与测试;
2) 基础资源的建立;
3) 基础物料信息梳理;
4) 设计BOM与制造BOM应用模型验证;
5) 根据图档数据整理预案进行图档数据归集和整理;
6) To be业务流程模板建立;
7) 开展系统用户及关键用户培训;
8) 启动系统二次开发人员培训及二次开发程序编写。
系统试运行与总体评估:08年3月-08年7月
按照分布实施原则,采用典型产品验证方法,试运行阶段主要选择了具有典型意义的30万千瓦和60万千瓦两台机组进行试点运行, 按照PLM项目总体实施方案和上线运行办法,PLM系统实施应用重点以图文档管理、设计BOM与制造BOM管理、业务流程管理、技术准备计划管理、CAPPERP集成管理为主线, 通过两台机组真实全面的业务和流程检验系统功能和项目方案,在试运行过程中对公司业务、相关流程、管理模型进行不断优化,从而形成符合东汽实际的技术开发管理、制造工艺管理、业务流程管理及系统集成的一体化集成平台,并将这种管理模式推广到其它机组项目上进行应用试运行,主要展开工作为:
1) 对客户化系统应用联调测试与评估;
2) 组织客户化系统培训;
3) 制定系统应用规范与用户化操作手册编制,操作AVI的录制;
4) 按数据整理预案跟进数据整理,充实系统资源;
5) 试运行上线技术蹲点支持;
6) 试运行总体评估,启动上线切换方案及上线动员。
系统全面上线:08年8月15日
根据公司PLM系统上线切换要求,通过试运行的总体评估,自切换通知之日起,所以新开工机组数据全面纳入PL系统运行,包含主要业务为:
1) 总师办技术准备计划全面纳入PLM系统管理;
2) 产品开发处新设计相关图纸、文件、总部套目录、子部套目录、设计BOM、业务单据、数据审会签流程、数据变更流程、图档与设计BOM发布全面纳入PLM系统;
3) 制造技术处制造BOM、工艺图纸、工艺路线、材料定额及两级工艺任务管理、工艺数据审会签、变更及发布流程全面纳入PLM系统;
4) 开放各业务部门新设计相关机组业务数据查询及报表权限,统一使用PLM系统发布的设计数据,各相关业务部门数据审会签流程、变更会签与发布流程全面纳入PLM系统管理;
5) 东汽各子公司与总厂相关图纸、文件、设计BOM、业务单据、数据审会签流程、数据变更流程、图档与设计BOM发布全面纳入PLM系统;
6) 通过专门接口,基于制造BOM对ERP系统、CAPP系统进行数据传递。
到目前为止,已经有38台机组数据及作业流程全面进行PLM系统。包括风电事业部、自控公司、表面工程公司。
5. 突出重点
汽轮机企业PLM系统实施是一个复杂工程,通过PLM系统的实施实现工厂电子数据权限管理、信息共享查询、图纸电子化管理、BOM管理、ERP集成等基本目标,实施总体目标中明确提出通过PLM系统的实施需要重点解决以下四个方面的问题:
1)促进新的产品设计体系建立,适应新的数据管理模式;
通过PLM系统的实施,建立产品设计工作平台,在新的平台系统上产品开发处及制造技术设计体系要适应产品数据无纸化、电子化管理、数据存储以及产品设计流程电子化管理的管理要求。新图纸体系的基本原则是“图纸与明细分离”。
不仅装配图纸的图面,将不出现明细信息,零件图也不再出现材料等信息,加强外流数据保密性管理要求,实现图、物料及材料的分离。即使旧版图纸电子化后原图面上的明细信息只作为参考,无论是在公司技术、质量方面,还是在公司制造、生产、服务方面,明细数据一律以PLM系统中BOM数据为准。
新体系基于PLM系统平台,要求产品设计由“新图纸设计”转到以“新物料的设计”为中心的设计体系,推行基于标准骨架体系的设计BOM构建思想,产品设计必须把保证“物料BOM准确性”的重要性提高到与保证“图纸上的尺寸外形技术条件等数据准确性”相同的高度。
在PLM系统平台上,产品设计工作流程进行无纸化、电子化管理,所有产品图纸、BOM数据形成的所有流程,包括设计、校对、审核、会签、审定、审批、批准及发布全部进行电子化管理、电子化签名,产品设计图纸、BOM数据一律以PLM电子信息为准,取消所有管理部门蓝图发放,车间采用白图发放,取消人工改图,更改采用直接收换,充分发挥电子数据的作用,推进工厂知识库管理目标。
2) 基于标准骨架体系的设计BOM管理与制造BOM自动衔接;
汽轮机设计与制造过程十分复杂,在进行产品研发的过程中,研发部门需要根据不同专业将产品划分成不同的部套目录,然后再由各个专业室进行部套的详细设计,进而产生整个产品的设计BOM。
在工艺和制造的过程中,制造技术部门,则根据产品的装配结构对设计产生的部套进行归类和划分,从而区分出需要分属于主体、附件和不参加总装的子部套,这样做可以方便加工、转运、装配工作的组织。因此,在每台新产品研发完成之后,设计人员需要花费大量精力将面向设计的BOM转换成面向制造的BOM,产生各种管理问题。
基于标准骨架体系的设计制造BOM转换方案,是实现从设计BOM向制造BOM转换的关键一步, 在PLM系统上建立起来的新设计体系促使产品设计数据扁平化,满足了实现“零件管理”要求。
产品设计数据“装配层物料BOM”采用“PBOM转换代码”、“模块归属”代码设计信息,满足“设计BOM”向“面向制造的BOM”自动转换要求。 产品设计新图纸体系中物料(产品设计的不同存在状态)的“衍生演变”过程标准化。
产品设计数据BOM增加“上传关系代码”,使物料“衍生演变”过程数字化。产品设计数据“装配层物料BOM ”增加包装属性“发运方式代码”,PLM系统计算,实现产品自动装箱,生成设计原始装箱清单。转换方案分成三步:
首先,根据机型骨架模板产生台分化的制造BOM;
然后,设计人员在部套设计BOM中填写转换代码;
最后,借助自动转换工具完成从设计制造BOM的转换。
在第一步中,设计人员事先根据制造结构将通用的制造骨架模板进行实例BOM模板的自动展开。例如:对于指定机型的机组必须包含指定数目的隔板组件。这一骨架模板描述了每台汽轮机必定包含的基本模块。
在第二步中,每当设计人员完成新大部套的设计之后,会在该部套到下层子部套之间的关系上输入转换代码,描述下层子部套哪些安装在主体上、哪些安装在附件上以及哪些是属于不参加总装的子部套,并指定拆分以后的结果如何分配到骨架的所属的模块上。完成转换代码工作之后通过审计流程将设计完工的部套传递到下游数据组,从而进入第三步。
在第三步中,数据组借助设计制造BOM转换工具,对已经补充转换信息的设计BOM部套结构进行拆分,从而区分出主体、附件和不参加总装的部分。再根据设计人员填写的模块信息将拆分之后的代码放到台分化骨架上。
通过上述三步,实现设计制造BOM的自动转换。