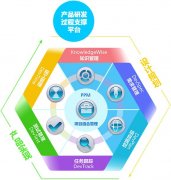
PLM拓展应用的实践与探索
九五甩图板CAD应用示范工程之后,在企业技术管理方面也逐渐产生了新的需求,先后有对电子图文档管理的需求(EDM),对工艺编制及工艺管理的需求(CAPP),对设计BOM管理及报表、设计过
产品应用
九五“甩图板”CAD应用示范工程之后,在企业技术管理方面也逐渐产生了新的需求,先后有对电子图文档管理的需求(EDM),对工艺编制及工艺管理的需求(CAPP),对设计BOM管理及报表、设计过程管理、更改过程管理的需求(PDM),后来逐步形成了设计和工艺一体化应用的需求及技术部门实现多BOM管理的需求,以及对产品质量及售后服务的需求。
从EDM、PDM到PLM,走过了十多年的发展历程,不但产品的核心应用功能不断得以加强和细化,而且其应用的外延性、系统的集成性、管理的精细化以及对管理的效益要求也越来越高,产品技术管理系统正从单一的、表面的、局部的示范应用转向多层次、深入的、全面的实际应用。
现在企业PLM应用无论是采用PDM+CAPP的系统集成技术,还是采用PLM设计工艺一体化技术,企业从实际应用中的图文档管理、产品BOM管理、设计过程管理、工艺过程管理、更改过程控制都能比较容易找到解决方案,应用难度也不大,更多企业的管理层希望PDM或PLM应用在企业的成本控制、管理效率提升、研发考核及企业知识管理等方面带来效益。
笔者是一线的PDM/PLM工作者,见证了部分企业在实践中从以上几个方面取得了良好的效果,而且越来越多的企业高层领导也开始关注这些方面的应用。为此撰文,总结几点经验,与大家分享。
一 从设计源头对成本进行控制
控制和管理业内有个公认的说法:产品80%的成本是在设计阶段决定的,产品75%的错误是设计阶段引起的。目前,制造业都面临激烈的市场竞争,早期按一定时期产品平均摊薄核算法,由于成本误差大,对于按订单的单台产品成本更是难以得到,不便于成本的准确和敏捷管理。因此,企业领导越来越迫切需要在技术阶段引入计划成本的概念,这也为技术部门提出了难题。有了PLM系统作为支撑,解决该问题才是可行的。
产品计划成本是所谓的“零利润成本”,“零利润成本”是产品报价和确定销售价格的基础。“零利润成本”主要由材料成本(包括主材和辅材)和加工费率(工时成本)两大主要因素构成,而物料清单(BOM)在PLM系统十分容易得到,核算工时的成本难度稍大,因为一般的企业工序、工时并不由工艺人员在技术文件中体现,而是由专门的人单独核算。
以下公式分别是产品材料成本和产品工时成本的模型:
产品材料成本=Σ自制件材料定额×材料价格+Σ辅料定额×辅料价格+Σ外购件数量×零件价格。
产品工时成本=Σ零件制造工时费用+Σ零件装配工时费用。
(注:零件计划工时费用=Σ工序×工序费率×工序时间,工序费率是指特定工序的计划价格)
在PLM系统生成设计BOM之后,工艺人员在BOM的基础上,搭建和维护产品制造BOM。制造BOM中记录了零部件的组成关系、每个零部件的材料用量以及生产加工过程中辅料的用量,PLM系统完整描述了产品的材料使用情况,对于材料成本的信息,尤其是产品的大部分主要材料的成本信息(各种型材、外购件和标准件),十分容易得到,剩下的就是主材公式的规范和使用问题,而对于辅助材料(焊条和油漆等),如果占的成本因素较大,也可以按此方法实现,如果占的成本比较小,对于设计材料成本的预算来说,就可以忽略。
同样,在工时的计算中,工序名称是技术内容,容易实现,难的就是工序费率和工序时间,这两个公式的规范和简化,直接影响到工时自动计算的应用和推广,也是影响成本预算问题的核心所在,但只要企业有足够的决心,是可以得到比较满意的结果的。
有了PLM这些基础数据,再通过和ERP(财务)系统的集成,材料引用企业ERP(财务)系统中的材料库,并参考其计划价格,工时采用参考工时或工艺卡片中的工时及ERP工时费率信息,通过公式自动计算就能对产品、部件、零件等进行“实时报价”和“快速成本预估”。
在PLM建立一套这样的模型后,并通过PLM提供的技术信息,成本预算就变得比较可行了。当然,建立准确度较高的工时模型也需要有一个过程,有了最初的模型,通过公式追溯,不断优化,并最终得到比较准确的预估成本,让成本预算有据可依。
二.技术资料管理无纸化
从设计、工艺到制造,技术数据全程电子化管理。通过PLM系统的实施,建立企业全程电子数据的审批管理电子化流程,保证电子数据的准确、及时归档,以此逐步规范数据管理和业务流程,实现真正的电子化管理,达到数据过程管理的无纸化。
PLM系统通过流程任务分配功能,实现对数据对象的检入,将需要设计审批的数据对象打包,执行预定义的适合该对象类的工作流程模板。相关的设计或工艺任务执行人接受该设计审批任务,审阅相关设计图纸的产品BOM结构,并进行对象或任务的文字、文件与红笔方式的批注,最后进行签字确认。
在任务执行过程中,PLM系统提供工作任务报警,当有任务达到当前桌面时用户可以在不启动PLM系统的状态下通过PLM的消息工具获得审批任务的消息,通过这种方式可以将任务自动分发到参与人员的工作列表中,实现流程的自动化,从而最大限度地提高流程的效率。
需要说明的是,工程设计管理模式的核心之一是设计管理的协同化,在PLM平台中,供应商、合作伙伴以及其他企业都可以参与这些自动化过程,从而提高了协作水平,实现技术部门及其供应商之间的协作。
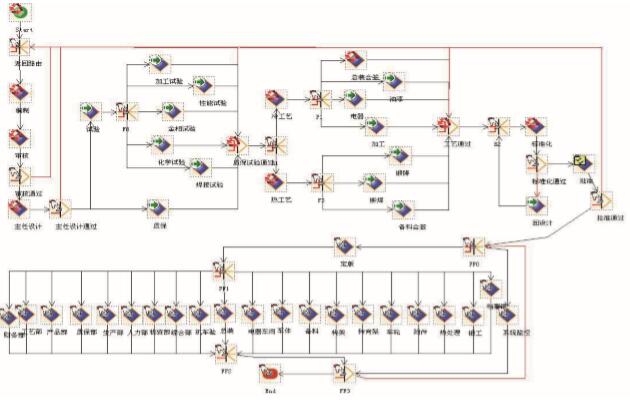
图2 产品图档签审自动分发流程示例图
大部分企业在努力实现技术部门之间无纸化信息流转的同时,增加了技术部门内部资料流动的及时性、准确性和一致性。但在车间及加工单位仍然需要按传统的方式提供蓝图,或直接从PLM中输出白图及各种技术更改单和联络单,因此,PLM的实施虽然加强了技术管理及规范,提高信息共享程度,减少了错误发生率,但对生产现场技术支持仍然没有改观,触摸屏的应用恰好填补了这一空白。
在河北的某装备制造业企业,在关键工位部署触摸屏,车间生产不再需要纸质的技术文件,大大增加了技术和工艺文件下发的时间,提高了管理效率。同时,数据更改的及时性和准确性也得到了根本性的保证,减少技术文件换版带来的种种弊病。
车间现场技术工人,只要根据当天的工单(来源于ERP或手工),输入要加工的物料编码,即可对该物料进行图纸浏览、工艺卡片浏览、质量标准浏览、其他技术标准浏览及更改通知的查看,配合PLM专有的触摸屏操作工具,十分方便地完成生产加工对技术文件的查看,目前该企业部署了30多台触摸屏设备,满足了近50个工位的使用需求,触摸屏应用效果非常好。以下是PLM触摸拼专用浏览界面:
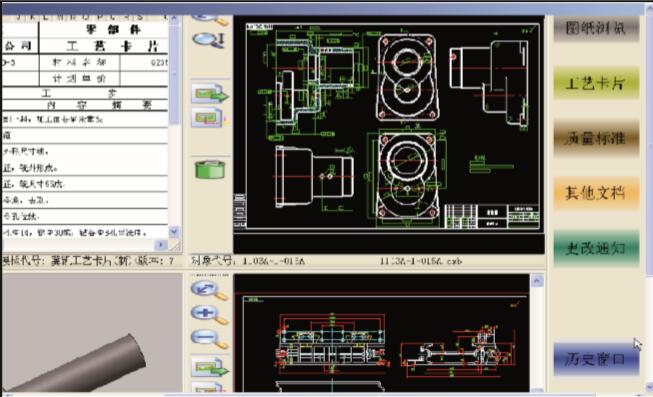
图3 PLM触摸屏客户端
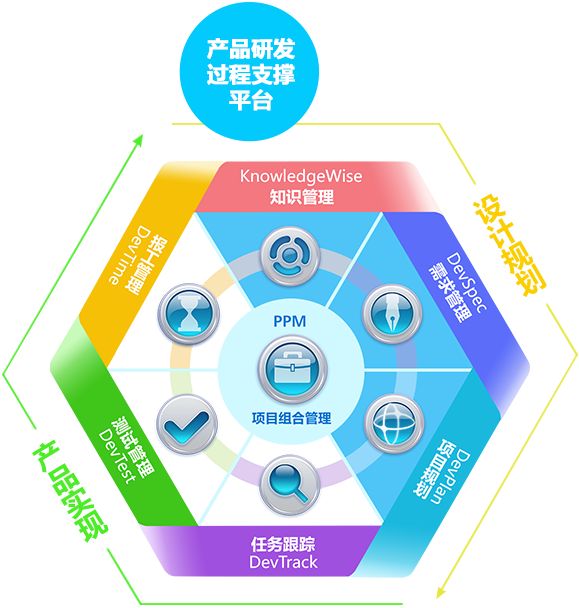
从EDM、PDM到PLM,走过了十多年的发展历程,不但产品的核心应用功能不断得以加强和细化,而且其应用的外延性、系统的集成性、管理的精细化以及对管理的效益要求也越来越高,产品技术管理系统正从单一的、表面的、局部的示范应用转向多层次、深入的、全面的实际应用。
现在企业PLM应用无论是采用PDM+CAPP的系统集成技术,还是采用PLM设计工艺一体化技术,企业从实际应用中的图文档管理、产品BOM管理、设计过程管理、工艺过程管理、更改过程控制都能比较容易找到解决方案,应用难度也不大,更多企业的管理层希望PDM或PLM应用在企业的成本控制、管理效率提升、研发考核及企业知识管理等方面带来效益。
一 从设计源头对成本进行控制
控制和管理业内有个公认的说法:产品80%的成本是在设计阶段决定的,产品75%的错误是设计阶段引起的。目前,制造业都面临激烈的市场竞争,早期按一定时期产品平均摊薄核算法,由于成本误差大,对于按订单的单台产品成本更是难以得到,不便于成本的准确和敏捷管理。因此,企业领导越来越迫切需要在技术阶段引入计划成本的概念,这也为技术部门提出了难题。有了PLM系统作为支撑,解决该问题才是可行的。
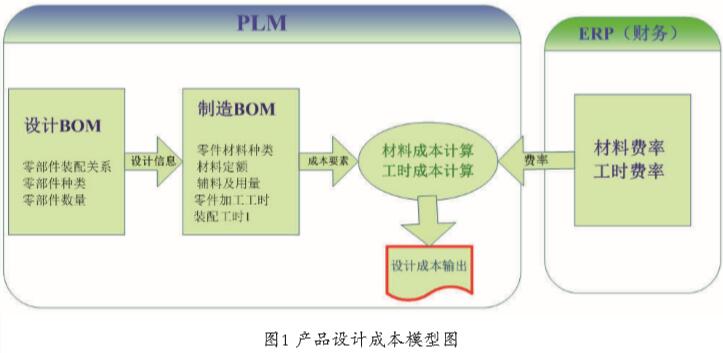
图1 产品设计成本模型图
产品计划成本是所谓的“零利润成本”,“零利润成本”是产品报价和确定销售价格的基础。“零利润成本”主要由材料成本(包括主材和辅材)和加工费率(工时成本)两大主要因素构成,而物料清单(BOM)在PLM系统十分容易得到,核算工时的成本难度稍大,因为一般的企业工序、工时并不由工艺人员在技术文件中体现,而是由专门的人单独核算。
以下公式分别是产品材料成本和产品工时成本的模型:
产品材料成本=Σ自制件材料定额×材料价格+Σ辅料定额×辅料价格+Σ外购件数量×零件价格。
产品工时成本=Σ零件制造工时费用+Σ零件装配工时费用。
(注:零件计划工时费用=Σ工序×工序费率×工序时间,工序费率是指特定工序的计划价格)
在PLM系统生成设计BOM之后,工艺人员在BOM的基础上,搭建和维护产品制造BOM。制造BOM中记录了零部件的组成关系、每个零部件的材料用量以及生产加工过程中辅料的用量,PLM系统完整描述了产品的材料使用情况,对于材料成本的信息,尤其是产品的大部分主要材料的成本信息(各种型材、外购件和标准件),十分容易得到,剩下的就是主材公式的规范和使用问题,而对于辅助材料(焊条和油漆等),如果占的成本因素较大,也可以按此方法实现,如果占的成本比较小,对于设计材料成本的预算来说,就可以忽略。
同样,在工时的计算中,工序名称是技术内容,容易实现,难的就是工序费率和工序时间,这两个公式的规范和简化,直接影响到工时自动计算的应用和推广,也是影响成本预算问题的核心所在,但只要企业有足够的决心,是可以得到比较满意的结果的。
有了PLM这些基础数据,再通过和ERP(财务)系统的集成,材料引用企业ERP(财务)系统中的材料库,并参考其计划价格,工时采用参考工时或工艺卡片中的工时及ERP工时费率信息,通过公式自动计算就能对产品、部件、零件等进行“实时报价”和“快速成本预估”。
在PLM建立一套这样的模型后,并通过PLM提供的技术信息,成本预算就变得比较可行了。当然,建立准确度较高的工时模型也需要有一个过程,有了最初的模型,通过公式追溯,不断优化,并最终得到比较准确的预估成本,让成本预算有据可依。
二.技术资料管理无纸化
从设计、工艺到制造,技术数据全程电子化管理。通过PLM系统的实施,建立企业全程电子数据的审批管理电子化流程,保证电子数据的准确、及时归档,以此逐步规范数据管理和业务流程,实现真正的电子化管理,达到数据过程管理的无纸化。
PLM系统通过流程任务分配功能,实现对数据对象的检入,将需要设计审批的数据对象打包,执行预定义的适合该对象类的工作流程模板。相关的设计或工艺任务执行人接受该设计审批任务,审阅相关设计图纸的产品BOM结构,并进行对象或任务的文字、文件与红笔方式的批注,最后进行签字确认。
在任务执行过程中,PLM系统提供工作任务报警,当有任务达到当前桌面时用户可以在不启动PLM系统的状态下通过PLM的消息工具获得审批任务的消息,通过这种方式可以将任务自动分发到参与人员的工作列表中,实现流程的自动化,从而最大限度地提高流程的效率。
需要说明的是,工程设计管理模式的核心之一是设计管理的协同化,在PLM平台中,供应商、合作伙伴以及其他企业都可以参与这些自动化过程,从而提高了协作水平,实现技术部门及其供应商之间的协作。
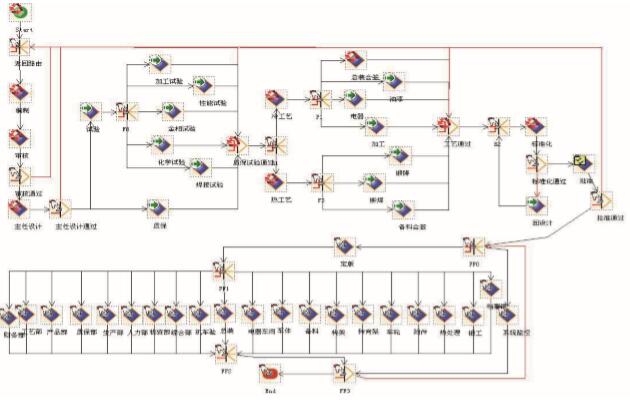
图2 产品图档签审自动分发流程示例图
在河北的某装备制造业企业,在关键工位部署触摸屏,车间生产不再需要纸质的技术文件,大大增加了技术和工艺文件下发的时间,提高了管理效率。同时,数据更改的及时性和准确性也得到了根本性的保证,减少技术文件换版带来的种种弊病。
车间现场技术工人,只要根据当天的工单(来源于ERP或手工),输入要加工的物料编码,即可对该物料进行图纸浏览、工艺卡片浏览、质量标准浏览、其他技术标准浏览及更改通知的查看,配合PLM专有的触摸屏操作工具,十分方便地完成生产加工对技术文件的查看,目前该企业部署了30多台触摸屏设备,满足了近50个工位的使用需求,触摸屏应用效果非常好。以下是PLM触摸拼专用浏览界面:
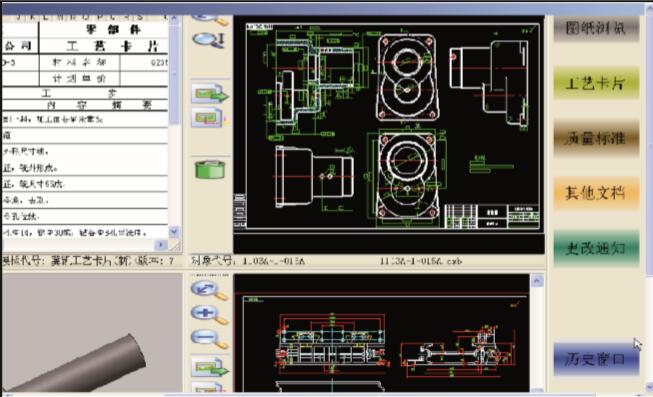
图3 PLM触摸屏客户端
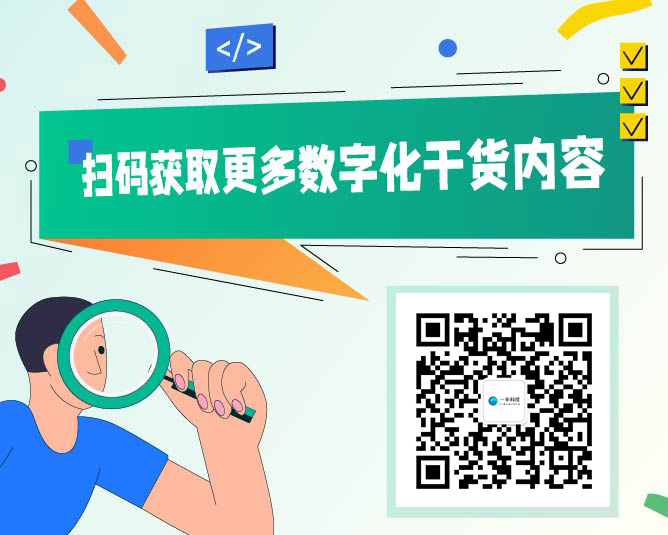