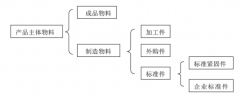
PLM助你实现企业物料标准化管理
随着产品研发数据化信息化的发展,制造企业ERP系统加主数据系统的模式已成为制造企业的主流业务系统应用模式。物料编码作为PLM系统的核心主数据,是ERP时代企业业务行为和业务管
产品应用
随着产品研发数据化信息化的发展,制造企业ERP系统加主数据系统的模式已成为制造企业的主流业务系统应用模式。物料编码作为PLM系统的核心主数据,是ERP时代企业业务行为和业务管理的基础。在企业的研发、生产、经营活动中,科学、合理、健全的物料编码体系才能保障数据信息规范传递、准确使用。
1 制造企业的物料分类
制造企业物料一般包括:产品主体物料、原辅材料及非产品用物料。
1.1 产品主体物料
产品主体物料可以是一台完整的产成品,也可以是组成完整产成品的不同种类的零部件,根据其特点可分为成品物料和制造物料,制造物料又可分为加工件、标准件、外购件,其中标准件包含标准紧固件和企业标准件。此类物料的共同点是均为有图件。产品主体物料分类如图1所示。
图1 产品主体物料分类
1.2 原辅材料
原辅材料包括金属材料和非金属材料两大类,具体分类见表1。
1.3 非产品用物料
非产品用物料包括主要固定资产、计量器具、工艺装配、劳保后勤等服务管理用物料。此类物料与产品数据关系不大,本文就不再详述。
2 物料编码规则
编码规则首先必须保证编码的唯一性和可扩展性的要求。物料的编码规则一般为有含义数字分类代码加无含义顺序流水码组成,可根据不同物料的数量及属性制定不同的编码规则。物料编码应可以明显进行区分,避免“一码多物”或“一物多码”现象而带来的使用、管理问题。
2.1 产品主体物料编码
产品主体物料编码属于赋意编码,即对编码的码段有明确的规则定义,赋予一定的含义。
2.1.1 成品物料
成品物料是制造企业最终出产的具有独立、完整功能的产品,是按照国家及行业等相关标准进行命名的产成品型号,产品型号包含产品分类代号、主要技术参数、结构特征等属性,具有规范性和通用性。
2.1.2 制造物料
(1)加工件
加工件具有按照图样分类编号规则制定的唯一图号编码。图样分类编号规则可采用十进位分类法,即将需要编号的图样或文件按其特征、结构或用途分为十级(大类),每级分十部(功能),每部分十类(特征),每类分十组(结构),根据产品本体物料所处层级及属性的不同,按照部、类、组进行划分,物料的特征、结构、用途等直接体现在了编码中。确定了制造物料的部、类、组,其顺序号可在PLM系统中按照顺序自动给出。
表1 原辅材料分类
产品主体物料编码的构成如图2所示。
图2 产品主体物料编码规则
一个功能为传动、涡轮类、链轮结构的部件,其物料编码可根据分类编号规则的级、部、类、组分别选择为5(部件)、2(传动)、4(涡轮类)、9(链轮结构),若顺序号为0001,则此部件的物料编码为5-249-0001。
(2)外购件
外购件指根据生产组织需要从外部采购,可直接作为产品零部件使用的物料。外购件在研发和生产组织过程中按照类别模块进行划分,实行标准化整合管理,合理减少外购物料品种和数量,提高物料的通用性,降低采购成本,提高产品质量可靠性。
外购件的编码规则如图3所示。
图3 外购件物料编码规则
外购件类别代号一律为“W”,分类代号按照表2进行选取。
(3)标准件
标准紧固件是由国家标准、行业标准规定了规格及要求的紧固零件,包括螺栓、螺母、螺钉、垫圈、挡圈、销钉等。
企业标准件是制造企业根据自身生产需求规定了企业代号,经优选在不同类型或同类型不同规格的产品中具有互换性且易于批量生产的零部件。
不论标准紧固件还是企业标准件,均以外购为主。将此类标准件从外购件中分离出来单独编码管理,可将标准件规格型号直接体现在编码中有利于快速选用。
表2 外购件分类
2.2 原辅材料物料编码
原辅材料的物料编码规则如图4所示。
图4 原辅材料编码规则
3 物料的标准化管理
物料编码体系是企业一体化管控的要求,也是信息化系统得到有效应用的基础。物料编码体系建立后,对体系的管控和维护,是基础数据标准化的一项重要工作,需要专门的人员负责审核编码的变更和新增申请,保持物料编码体系的专业性和完整性。
由于与产品数据相关的物料性质不同,物料编码体系的管理维护分为三大部分,一是成品物料的管理,二是加工件物料的管理,三是外购件、标准件和原辅材料等物料的管理。
成品物料即产品型号应由技术管理部门专项管理,制造企业在产品研发立项阶段进行策划。有国家/行业标准规定的产品,按照相关标准进行产品型号命名;暂时没有国家/行业标准规定的新领域产品由制造企业按照产品型号命名规范自行编制产品型号,若其命名不符合后来发布实施的标准要求,后续研发的同系列产品按照相关国家/行业标准进行命名。成品物料申请需有完整的审批流程,符合企业产品研发计划的要求,充分体现产成品特点。制造物料中的加工件物料管理关键是要建立零部件类型库。对零部件按照类型进行类别划分并制定相应分类属性,方便技术人员进行检索。对应到设计过程中,在库的数据基础上可以通过属性定义查找到最接近的零部件,增加零部件的重用率,避免一物多码的现象,减少物料冗余,加快设计进度,提高履约效率。
外购件、标准件和原辅材料等物料主要通过数据库进行统一管理。对于外购件按照功能进行划分和类别限定,并将物料描述、主要参数、型式、规格、生产厂家等信息进行属性维护,方便技术人员选用;根据标准化原则,优化标准件的种类规格,要求在相同结构下使用同一类型和规格的标准件。并通过系统设置,对标准件库的使用情况进行排序,推荐技术人员采用借用频次较高的标准件,最大限度减少非推荐物料的使用,提高设计开发的继承性和产品标准化程度;针对原辅材料可通过梳理原材料物料数据,与采购数据、生产代料明细对比分析,对原材料物料实现优先序列分级管理,通过系统检索,推荐优先选型物料序列,指导设计选材,合理采购。
为避免产品研发时出现使用不规范的物料情况,对外购件、标准件和原辅材料等物料均需进行有效的规范和控制,设置专门的物料准入流程:
需求部门首先在PLM系统查重,若无此编码则发起“物料申请”流程,经采购主管、标准化管理员、部门经理等责任人员流程审批,在同意使用后,由标准化管理员在相应物料库中创建,并维护相关属性,才可以使用;或者在标准化管理员的建议下,更换为更为合理的通用化或模块化设计结构,选用推荐范围内物料。
各类物料数据库中物料的维护实行分序列管理,分为推荐序列、可选序列和禁用序列三类,技术人员对计划使用物料通过系统筛查,优选推荐序列内物料,其次为可选序列。物料序列每年随着物料数据的使用量更新进行调节,对连续三年以上未被借用或相应标准规范变更不再使用物料设置“物料退出”流程,纳入禁用序列管理。制造企业通过将物料标准化管理规范和PLM系统相融合,建立物料数据选型、录入、筛选、封存等全线管理机制,形成物料数据动态管理模式,合理减少流通中物料数据的数量,提高物料的通用化程度,降低设计、采购和管理成本。物料标准化工作是企业长期发展的战略基础,不断拓展细化物料标准化管理整合范围,用尽可能少的优选物料,配制出多规格、多品种的产品,更好地满足市场需求。
1 制造企业的物料分类
制造企业物料一般包括:产品主体物料、原辅材料及非产品用物料。
1.1 产品主体物料
产品主体物料可以是一台完整的产成品,也可以是组成完整产成品的不同种类的零部件,根据其特点可分为成品物料和制造物料,制造物料又可分为加工件、标准件、外购件,其中标准件包含标准紧固件和企业标准件。此类物料的共同点是均为有图件。产品主体物料分类如图1所示。
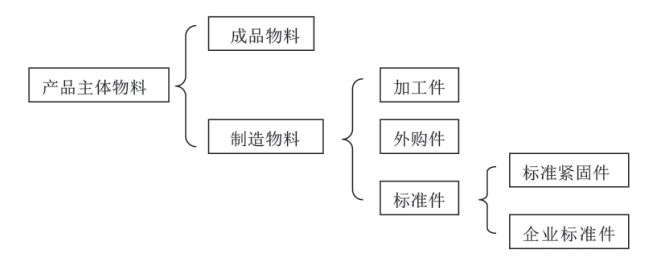
图1 产品主体物料分类
1.2 原辅材料
原辅材料包括金属材料和非金属材料两大类,具体分类见表1。
1.3 非产品用物料
非产品用物料包括主要固定资产、计量器具、工艺装配、劳保后勤等服务管理用物料。此类物料与产品数据关系不大,本文就不再详述。
2 物料编码规则
编码规则首先必须保证编码的唯一性和可扩展性的要求。物料的编码规则一般为有含义数字分类代码加无含义顺序流水码组成,可根据不同物料的数量及属性制定不同的编码规则。物料编码应可以明显进行区分,避免“一码多物”或“一物多码”现象而带来的使用、管理问题。
2.1 产品主体物料编码
产品主体物料编码属于赋意编码,即对编码的码段有明确的规则定义,赋予一定的含义。
2.1.1 成品物料
成品物料是制造企业最终出产的具有独立、完整功能的产品,是按照国家及行业等相关标准进行命名的产成品型号,产品型号包含产品分类代号、主要技术参数、结构特征等属性,具有规范性和通用性。
2.1.2 制造物料
(1)加工件
加工件具有按照图样分类编号规则制定的唯一图号编码。图样分类编号规则可采用十进位分类法,即将需要编号的图样或文件按其特征、结构或用途分为十级(大类),每级分十部(功能),每部分十类(特征),每类分十组(结构),根据产品本体物料所处层级及属性的不同,按照部、类、组进行划分,物料的特征、结构、用途等直接体现在了编码中。确定了制造物料的部、类、组,其顺序号可在PLM系统中按照顺序自动给出。
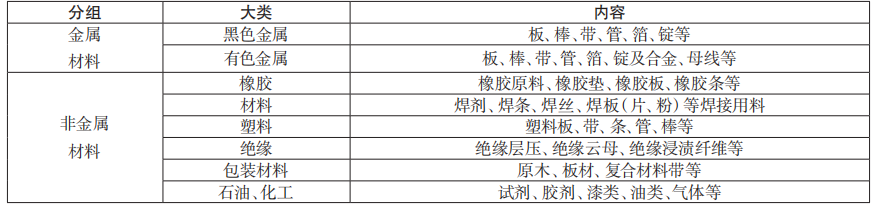
表1 原辅材料分类
产品主体物料编码的构成如图2所示。
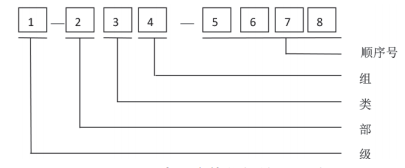
图2 产品主体物料编码规则
(2)外购件
外购件指根据生产组织需要从外部采购,可直接作为产品零部件使用的物料。外购件在研发和生产组织过程中按照类别模块进行划分,实行标准化整合管理,合理减少外购物料品种和数量,提高物料的通用性,降低采购成本,提高产品质量可靠性。
外购件的编码规则如图3所示。
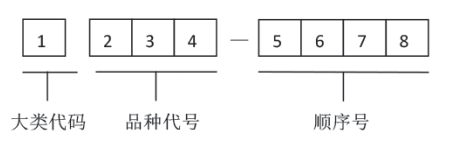
图3 外购件物料编码规则
(3)标准件
标准紧固件是由国家标准、行业标准规定了规格及要求的紧固零件,包括螺栓、螺母、螺钉、垫圈、挡圈、销钉等。
企业标准件是制造企业根据自身生产需求规定了企业代号,经优选在不同类型或同类型不同规格的产品中具有互换性且易于批量生产的零部件。
不论标准紧固件还是企业标准件,均以外购为主。将此类标准件从外购件中分离出来单独编码管理,可将标准件规格型号直接体现在编码中有利于快速选用。
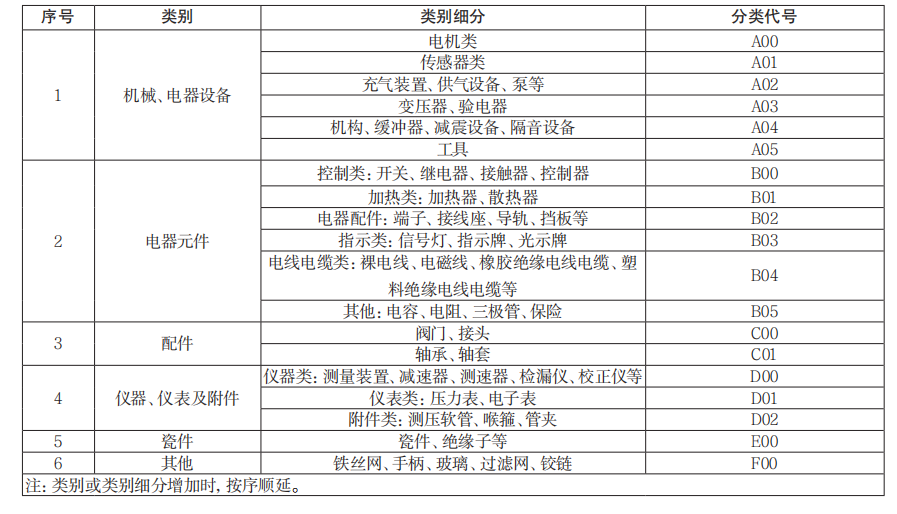
表2 外购件分类
原辅材料的物料编码规则如图4所示。
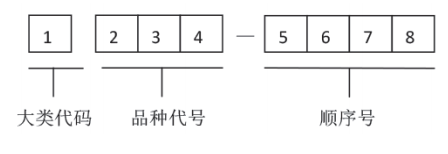
图4 原辅材料编码规则
3 物料的标准化管理
物料编码体系是企业一体化管控的要求,也是信息化系统得到有效应用的基础。物料编码体系建立后,对体系的管控和维护,是基础数据标准化的一项重要工作,需要专门的人员负责审核编码的变更和新增申请,保持物料编码体系的专业性和完整性。
由于与产品数据相关的物料性质不同,物料编码体系的管理维护分为三大部分,一是成品物料的管理,二是加工件物料的管理,三是外购件、标准件和原辅材料等物料的管理。
成品物料即产品型号应由技术管理部门专项管理,制造企业在产品研发立项阶段进行策划。有国家/行业标准规定的产品,按照相关标准进行产品型号命名;暂时没有国家/行业标准规定的新领域产品由制造企业按照产品型号命名规范自行编制产品型号,若其命名不符合后来发布实施的标准要求,后续研发的同系列产品按照相关国家/行业标准进行命名。成品物料申请需有完整的审批流程,符合企业产品研发计划的要求,充分体现产成品特点。制造物料中的加工件物料管理关键是要建立零部件类型库。对零部件按照类型进行类别划分并制定相应分类属性,方便技术人员进行检索。对应到设计过程中,在库的数据基础上可以通过属性定义查找到最接近的零部件,增加零部件的重用率,避免一物多码的现象,减少物料冗余,加快设计进度,提高履约效率。
外购件、标准件和原辅材料等物料主要通过数据库进行统一管理。对于外购件按照功能进行划分和类别限定,并将物料描述、主要参数、型式、规格、生产厂家等信息进行属性维护,方便技术人员选用;根据标准化原则,优化标准件的种类规格,要求在相同结构下使用同一类型和规格的标准件。并通过系统设置,对标准件库的使用情况进行排序,推荐技术人员采用借用频次较高的标准件,最大限度减少非推荐物料的使用,提高设计开发的继承性和产品标准化程度;针对原辅材料可通过梳理原材料物料数据,与采购数据、生产代料明细对比分析,对原材料物料实现优先序列分级管理,通过系统检索,推荐优先选型物料序列,指导设计选材,合理采购。
为避免产品研发时出现使用不规范的物料情况,对外购件、标准件和原辅材料等物料均需进行有效的规范和控制,设置专门的物料准入流程:
需求部门首先在PLM系统查重,若无此编码则发起“物料申请”流程,经采购主管、标准化管理员、部门经理等责任人员流程审批,在同意使用后,由标准化管理员在相应物料库中创建,并维护相关属性,才可以使用;或者在标准化管理员的建议下,更换为更为合理的通用化或模块化设计结构,选用推荐范围内物料。
各类物料数据库中物料的维护实行分序列管理,分为推荐序列、可选序列和禁用序列三类,技术人员对计划使用物料通过系统筛查,优选推荐序列内物料,其次为可选序列。物料序列每年随着物料数据的使用量更新进行调节,对连续三年以上未被借用或相应标准规范变更不再使用物料设置“物料退出”流程,纳入禁用序列管理。制造企业通过将物料标准化管理规范和PLM系统相融合,建立物料数据选型、录入、筛选、封存等全线管理机制,形成物料数据动态管理模式,合理减少流通中物料数据的数量,提高物料的通用化程度,降低设计、采购和管理成本。物料标准化工作是企业长期发展的战略基础,不断拓展细化物料标准化管理整合范围,用尽可能少的优选物料,配制出多规格、多品种的产品,更好地满足市场需求。
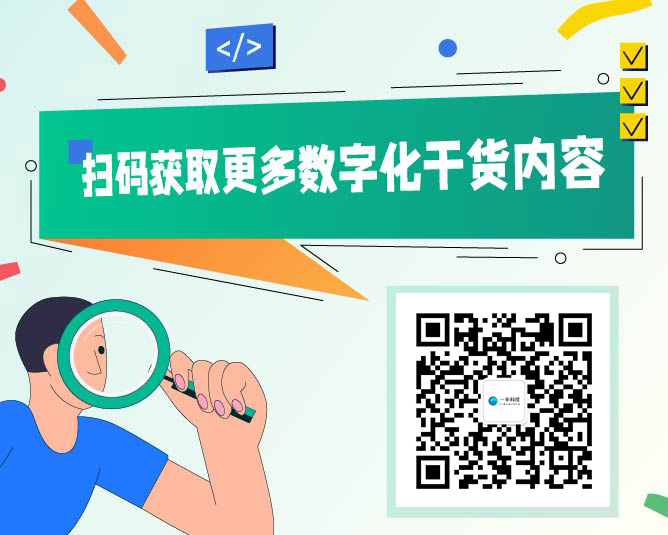
热门关键词